Profimach PGCH-180CNC -Series
Center-hole and center-cone Grinding Machine
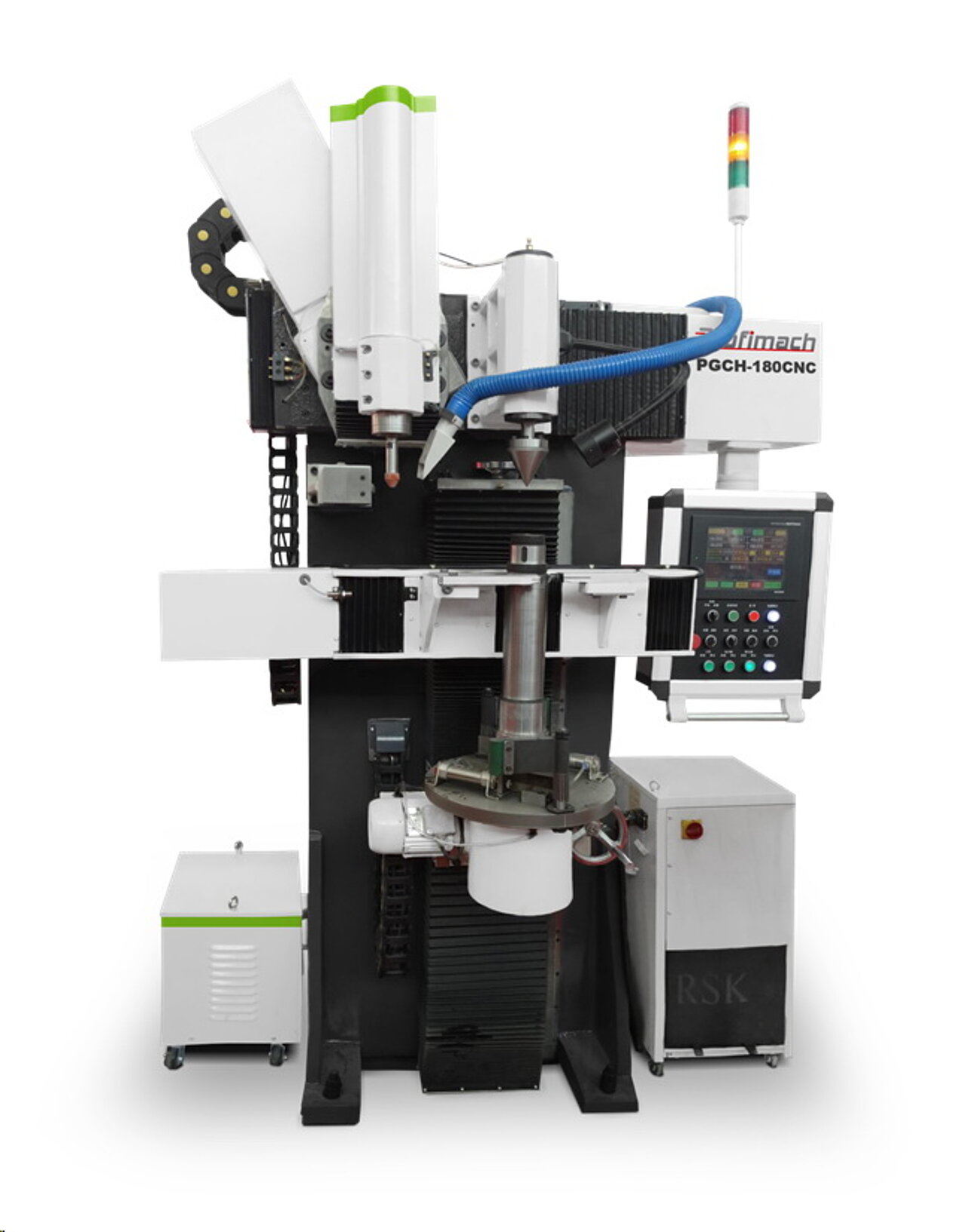
Profimach CNC Centre Hole Grinding Machine - Centre Grinding Machines
In pursuit of Higher Center Accuracy
There is an ever-increasing demand for higher workpiece accuracies.
Running on the dead centre tip of the external grinder the centre bore forms a plain bearing that directly effects the roundness of ground external diamters. For perfect results the taper of the centre bore must be round and co-axial with the centre bore at the other end of the workpiece.
After heat treatment the workpiece centre bores are often out of round or oval, out of alignment, covered with scale and too rough. To obtain good results in cylindrical grinding the centre bores must be ground or lapped by a Centre Grinding Machine before they are presented to the cylindrical grinding machine.
We offer Quality Center Grinding Machines at Affordable prices.
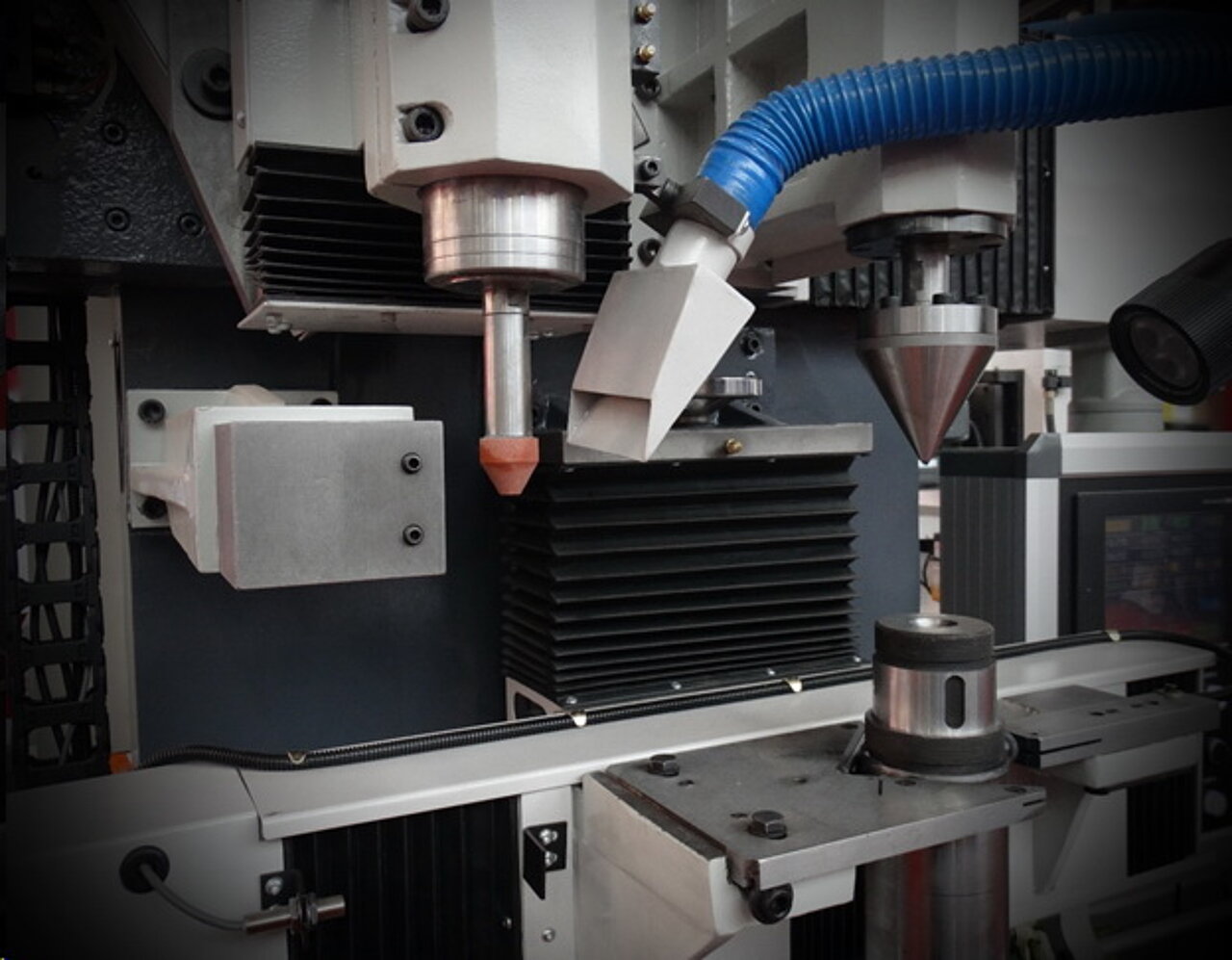
Accuracy of our Profimach PGCH-CNC:
Center hole cone angle: 60°+- 4μm
Surface roughness: ≤Ra0.4
Runout of the external circle to the center hole: ≤0.002mm
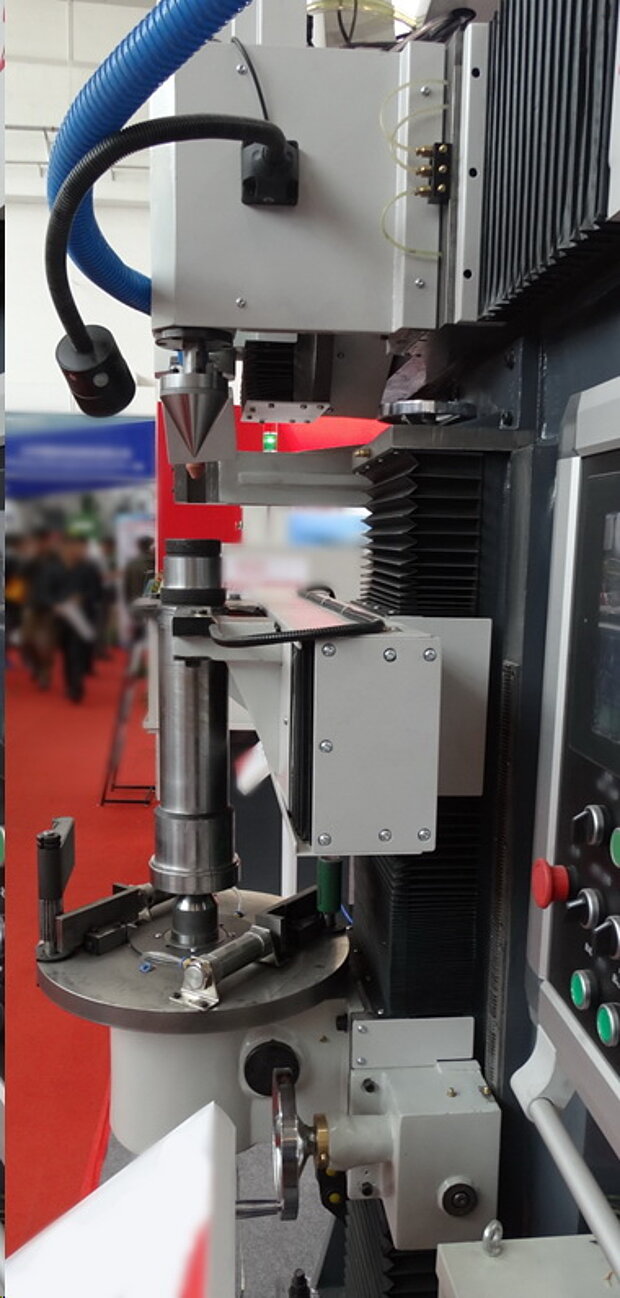
Profimach Centre Hole Grinding Machine
Treatment for Higher Precision
Profimach Centre Hole Grinding Machine are designed and perfected to produce just this, truly circular, geometrically accurate and precisely aligned center holes or center cones in components either in /soft or hardened condition.
Profimach PGCH-180CNC-Series of Center-hole and center-cone grinders not only make poor centers again precise but can move them as required to the optimum position
– for example, onto the axis of a gear halfway along a shaft bent during hardening.
Some of the benefits;
- When a subsequent external grinder – cylindrical, gear, spline, thread and its dead centers are in good condition, runout less than 0.001 mm can be obtained on work whose centers have been center ground with our Profimach grinder
- Subsequent grinding times are DRAMATICALLY reduced.
- Even case-depth can be assured on important surfaces.
- Subsequent roundness and concentricity checks have known bases.
- When center condition is unknown, inspection charts and diagrams are purely speculative.
- Full and correct contact between work and dead centers prolongs the principle of planetary grinding life of expensive carbide centers.
- Good center holes reduce drastically the vibrations in next operations
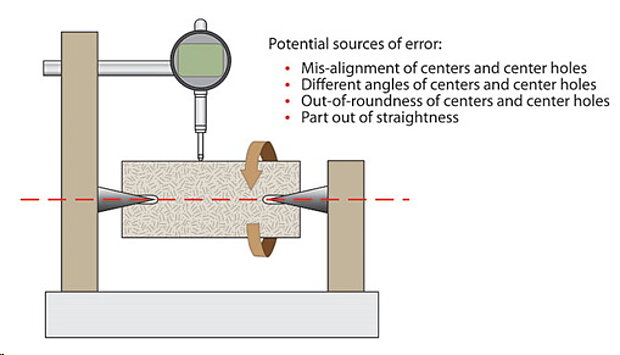
Profimach PGCH-180CNC
Series of Center-hole and center-cone Grinding Machine
Treatment for Higher Precision
Profimach Centre Hole Grinding Machine are designed and perfected to produce just this, truly circular, geometrically accurate and precisely aligned center holes or center cones in components either in /soft or hardened condition.
Profimach PGCH-180CNC-Series of Center-hole and center-cone grinders not only make poor centers again precise but can move them as required to the optimum position
– for example, onto the axis of a gear halfway along a shaft bent during hardening.
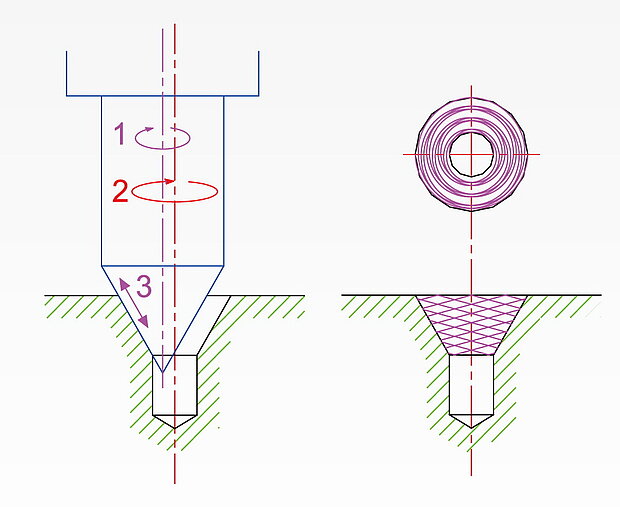
Some of the benefits;
- When a subsequent external grinder – cylindrical, gear, spline, thread and its dead centers are in good condition, runout less than 0.001 mm can be obtained on work whose centers have been center ground with our Profimach grinder
- Subsequent grinding times are DRAMATICALLY reduced.
- Even case-depth can be assured on important surfaces.
- Subsequent roundness and concentricity checks have known bases.
- When center condition is unknown, inspection charts and diagrams are purely speculative.
- Full and correct contact between work and dead centers prolongs the principle of planetary grinding life of expensive carbide centers.
- Good center holes reduce drastically the vibrations in next operations
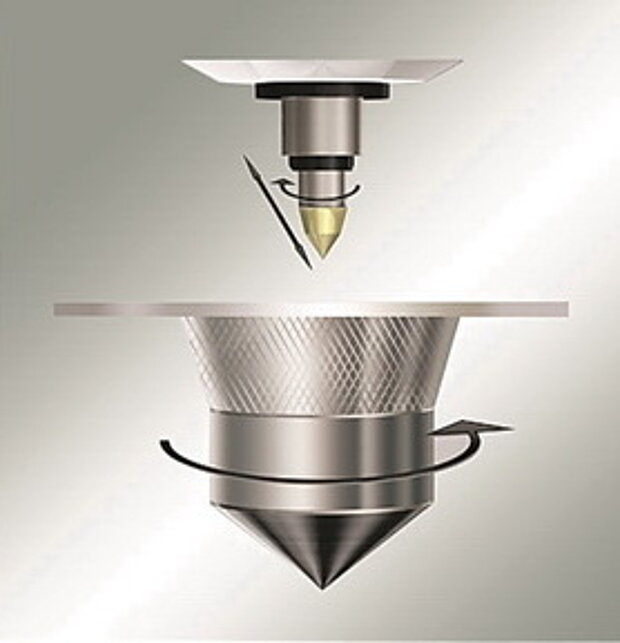
Operating principle
Profimach: center hole grinding machine- center cone grinding machine
The grinding cone dressed accurately to a 60 ° included angle is given three motions simultaneously to produce the desired result.
A Rotary motion of the grinding cone about its own axis, a rotary contra-sense rotation of the workpiece, coupled with a linear motion 30° angular with the spindle axis while the workpiece is held stationery on a bottom dead center and a 3-point self-centering V-vice.
Due to the three simultaneous grinding motions, the profimach fabricates a homogeneous cross-grinding pattern with microscopic oil pockets that form a constant oil film between the workpiece and dead center of the cylindrical grinding machine. This prevents dry running and seizing of the dead center and eliminates an additional source of error for high quality cylindrical grinding
Specifications and main technical parameters:
Items and specifications | PGCH-180/72CNC | PGCH-180/160CNC |
---|---|---|
Clamping workpiece diameter range | φ20-φ180 mm | φ30-φ180 mm |
Workpiece length range | 100-1000 (optional 1500) mm | 100-1000 (optional 1500) mm |
Max. Rotating diameter | φ300 mm | φ350 mm |
Center hole cone | 60° | 60° |
Maximum diameter of center hole cone | φ72 mm | φ160 mm |
Minimum diameter of center hole guide hole | φ2 mm | φ2 mm |
Maximum workpiece weight | 200 kg | 200 (250) kg |
Spindle speed and power | 40000(r/min)1.9kw | 40000(r/min)2.5kw |
Grinding wheel reciprocating stroke | 0-12mm | 0-5 mm (Maximum stroke 50mm) |
Grinding head up and down stroke (Z-axis) | 120 mm | |
Rotate speed of workpiece | 35(r/min) | 35(r/min) |
Grinding wheel diameter | φ30 mm, φ17mm | |
Rapid feed (X,Z,W,U) | 1800mm/min | 1800mm/min |
Z axis feeding speed | 0.001-5 mm/S | 0.001-5 mm/S |
Machine total power | 9.75kw | 7.75kw |
X axis repeated positioning accuracy | 0.003 | 0.003 |
Overall dimensions (L*W*H) | 1250*1040*2250 mm | 1450*1120*2250 mm |
Gross weight | 2650kg | 2940kg |
Auto centering device
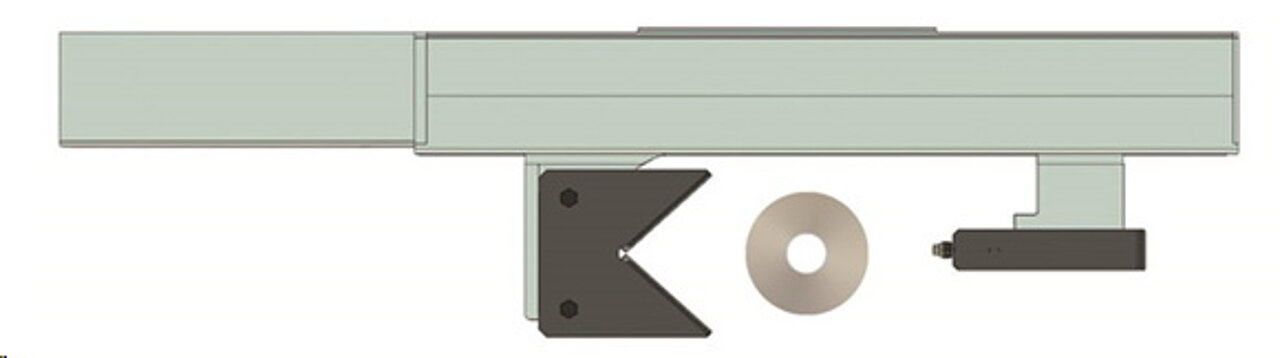