Profimach® Deep Holes drilling Machines
High quality affordable deep hole machines
These high precision deep hole drilling machines, BTA and gundrilling machines have been specially developed and improved in recent years.
All essential castings are made of high grade of cast iron that is stress relieved through annealing to eliminate internal stress. With the greatest stiffness and stability of the castings, these machines are suitable for precision deep hole working.
These deep hole drilling, BTA and gundrilling machines are offered with twofull-year limited warranty for mechanical and electrical parts.
Small Diameter BTA deep hole drilling machines
diameter till 100 mm
Medium Dia. BTA deep hole drilling machine
Diameter 30 - 350 mm
Heavy Duty BTA deep hole drilling machine
till diameter 750 mm
BTA deep hole drilling is a process that accurately drills holes from 20 – 650 mm in diameter with higher feed rates.
BTA drilling uses external coolant introduction and internal chip removal for precision drilling performance, even at extreme depths-to-diameter ratios.
6000 mm profimach BTA boring and drilling Machine
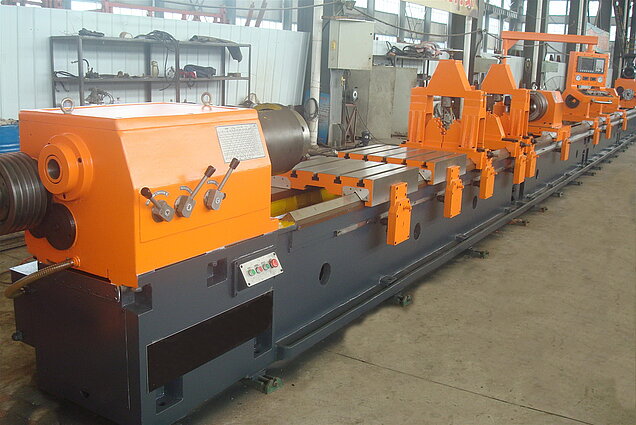
BTA drilling
BTA drilling is a deep hole drilling process that uses a specialized drilling tool on a long drill tube to produce deep holes in metal, from holes with a diameter of 20 mm and larger, up to depth-to-diameter ratios of 400:1. BTA drilling is the most effective method of drilling deep holes, as it is a cleaner, more reliable and capable process than conventional twist drills, and can achieve larger diameters and higher feed rates than the alternative gundrilling.
BTA drilling tool heads are threaded or mounted onto long drill tubes, and use multiple cutting surfaces on a single tool to remove chips efficiently, exhausting them using high-pressure coolant through holes in the tool head, then out the drill tube and through the machining spindle. BTA tooling is available in brazed or inserted carbide configurations.
BTA stands for Boring and Trepanning Association, and is also sometimes referred to as STS (single tube system) drilling, as it uses one single drill tube for the BTA tool, compared to other processes such as ejector drilling, which use two.
BTA Drilling vs Gun Drilling
BTA drilling can achieve drill feed rates of typically 5-7 times faster than gundrilling at the same diameter, due to the tool design, more efficient chip exhaust, and machine design and power. BTA drilling machines introduce coolant around the tool head, and evacuate chips through the drill and machine spindle, compared to gundrilling, where coolant is introduced internally and chips exit through an external groove. BTA drilling is VERY effective in holes from 20 – 300 mm (till 650 mm) , a greater size range than gundrilling.
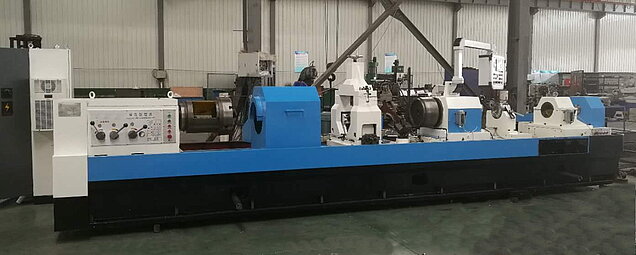
Pull Boring Highlights the Capability of Deep Hole Making
Pull boring enables users to achieve remarkable straightness in deep holes
Because the ability to make deep holes effectively and efficiently is critical in many applications, deep hole technology is one of the most highly developed sectors in metalworking. It covers a diverse range of processes and methodologies.
Although our deep hole drilling boring machines are designed for the special needs of creating holes through long workpieces, they have the flexibility to perform a variety of operations such as boring, counterboring, trepanning, roller burnishing and pull boring.
As an example of how deep hole technology has mastered some of its most extreme challenges, Profimach points to one particularly interesting technique: pull boring, which enables users to achieve remarkable straightness in deep holes. A variation of this technique is also effective when maintaining consistent wall thickness (in long, cast pipes, for example) is top priority.
As its name implies, pull boring involves pulling a cutter through an existing hole. Pull boring is usually performed on the same machine that created the original hole. In this case, a boring bar is inserted all the way through the existing hole. After emerging at the opposite end, the bar is fitted with a single-point pull boring head. The bar is then engaged in the tool drive mechanism and drawn back through the workpiece. The bar rotates in one direction, while the workpiece is rotated in the opposite direction by the work spindle. The tooling head holds a carbide insert of the appropriate grade and style for the workpiece material. This insert functions much like an ID turning tool, enlarging the original hole slightly as it is pulled into the workpiece. Coolant pumped around the boring bar channels chips up and out through its hollow center to aid metal removal and protect the surface.
Hole drift tolerances achieved by pull boring can be less than 0.08 mm/meter of workpiece length, if material, tooling and process conditions are favorable. However, reaching this level of straightness may require several passes.
For concentricity, a multi-point pull-boring head is used instead of a single-point tool. A multi-point tool typically has between two and six inserts. Wear pads are located in front of the inserts so that the existing ID of the bore provides support during cutting. In contrast, a single-point head is supported by the finished bore ID, so wear pads are located behind the insert.
Pull boring involves several nuances. For example, it is customary to make the original hole by boring halfway through the part, turning it end for end and boring the second half of the hole. This practice reduces the overall out-of-straightness condition in the resulting hole because each half of the bore will show less drift compared to a hole bored all the way through in a single pass. Thus, pull boring has a “head start” in its straightening action.
Pull boring can be applied to any part that a deep hole machine can accommodate. The only limit on part length is the length of the deep hole machine. Likewise, pull boring benefits from the same qualities of accuracy and rigidity in the deep hole machine that affect the original boring operation. In addition, sensing the rate and pressure of coolant flow, which the Unisig machines do automatically, enables users to protect workpieces and cutting tools by closely monitoring cutting conditions during pull boring.
A special accessory that makes pull boring more efficient is the lantern chuck. A drum-shaped device with openings on opposite sides, the lantern chuck is installed at the workpiece headstock end of the machine. The side openings make it easy to install and align a guide bushing for the pull boring tool. The lantern chuck also eliminates the need to machine a special pilot hole otherwise required so that the pull boring tool enters the workpiece on center.
Advances in deep hole technology will strenghten the capability of specialist shops while widening its use in general metalworking. By providing complete machining systems, tooling, coolant, accessories and process know-how, Profimach says it is ready to support customers following either trend.
Deep hole drilling and boring machine
Deep hole drilling and boring machines produced for Profimach are adopting internal chip-discharging strategy (BTA), which handles diameter from Φ30mm to Φ100mm (drilling), our deep hole machine's drilling, boring and rolling functions are applicable to propeller, landing gear and ejection seat; various barrels in military use; Our deep hole drilling and boring machine's boring diameter ranges from Ф40mm to Ф250mm, with maximum length - 10m.
Our maximum boring machine can handle boring diameter – 1250mm.
Accuracy of deep hole drilling and boring machine:
Drill hole: hole accuracy IT9-IT11, hole roughness: Ra6.3~Ra12.5um
Rough bore: hole accuracy IT8-IT9, hole roughness: Ra3.2~Ra6.3um
Fine bore: hole accuracy IT7-IT9, hole roughness: Ra1.6~Ra3.2um
Rolling and pressing: hole accuracy IT6-IT7, hole roughness: Ra0.4~Ra0.8um
Hole straightness: every meter less than 0.5mm
Drill hole range: 30mm~120mm
Bore hole range: 40mm-1200mm (different model)
Drill max depth: 18meters
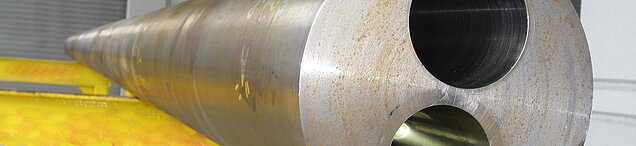