Rolling Mill equipment: CNC Roll Lathe
HEAVY DUTY CNC-TURNING LATHES FOR TURNING OF CAST IRON ROLLS
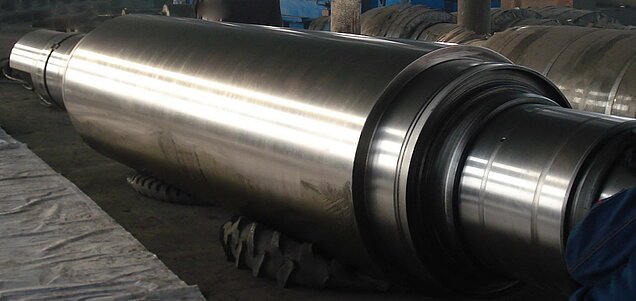
PTR-CNC-Series:
2nd-Generation CNC Roll Turning Lathe
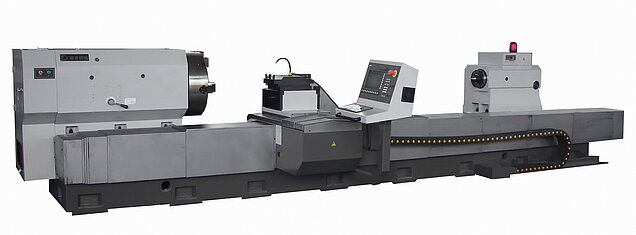
PTR-CNC-Series: CNC Roll Turning Lathe
Monoblock casting bed, with 4 hardened and grounded box guideways with double guideway confguration and with good rigidity and high accuracy. Separate feeding guide rail and tailstock guide rail reduces the interference of the component and makes the chip removal more convenient.
This series combines a maximum fexibility (carriages crossing capability) with the maximum rigidity, accuracy and durability. Suitable for high speed steel roll and high boron steel roll, laser roll and ordinary roll precision machining. Lathe bed is made of box Structure MEEHANITE vibration absorbing casting.
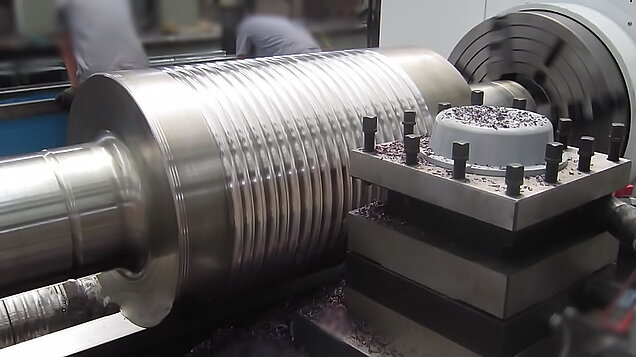
General characteristics 4 guideways lathes
These machines are designed for medium-heavy duty tasks (turbine shafts, hydraulic cylinders, wind turbine masts and so on). Profimach CNC lathes are really multitask centres, suited for high performed turning, boring, milling and grinding operations. The machine’s ergonomic feature allows the operator a good visibility throughout the various stages of machining, as well as eases of clamping, and check the product once it is finished. Steady rest must never be replaced during the full operation. Long shafts finished in one single set-up with only one clamping.
LATHES WITH BOX GUIDEWAYS
In comparison with linear guideways with rollers, box guideways have a significantly larger bearing face between the two mounted carriages and the machine bed. This means that the vibrations which are generated during the cutting process at the cutting edge are more effectively transmitted into the machine bed which, due to its high mass and damping characteristics, is extremely effective at absorbing them. This extends the life of tools, and helps them run more smoothly, resulting in better-quality surfaces on the workpiece and better cutting performance. The greater surface area also means that significantly heavier workpieces can be mounted and moved. Additional advantages of box guideways are their extreme durability and low sensitivity to collision damage (“crash situations”).
CNC Roll Turning lathe
Heavy duty automated machining.
The CNC Roll turning Lathe is the ultimate replacement solution for Manual Lathes used by Steel Plants in the Roll Shop for Roll machining and pass cutting. Available in various Models, the CNC roll turning lathes drive a huge improvement in productivity, reduce the need for labor, eliminate manual errors and reduce the space required for turning operation in machining the Rolls.
The CNC Roll turning lathes from Profimach provide an economical solution to improve the quality of end product, productivity of the manufacturing process and thus adds to your profitability.
Machine Tools Features
- High Torque capacity at Head stock Face plate
- Zero backlash with ball screw
- Provision for higher cutting force
- 4 Guide way Lathe Bed
- Perfect and Right Dimension of Bearing and Moving Parts
- Telescopic cover to protect guideways
- Rough and Finish Machining is achieved in the Lathe and with Siemens, Syntec, Mitsubishi,..CNC System programming
- Remote diagnostics with ethernet ready machine
Advantages
- Reduced downtime by eliminating the manual changing of rolls
- Faster machining
- Idel for machining split pass forms
- Easily replaces more than 5 manual lathes and frees up the space and complexity on the shop floor
- Suaitable for composite and carbide rolls
- Significantly reduces the operation time and Operator time
- Cost savings through reduced inventory of rolls
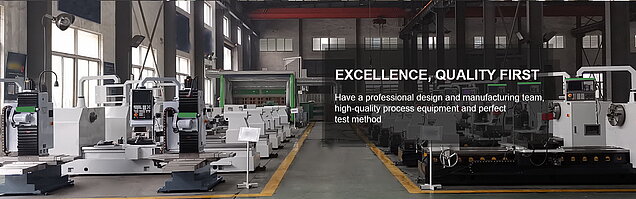
PTR-CNC Series CNC Roll turning lathes
High Rigid CNC Roll Turning Lathe - 2nd Generation
PTR- 90CNC - Series : maximum load = 4 Ton
PTR-110CNC - Series : maximum load = 8 Ton
PTR-145CNC - Series : maximum load = 20 Ton
PTR-CNC - Series : CNC Roll Turning Lathes
4-Guideway Roll Turning Lathes - Seperate guides for tailstock and Steady rests
PTR-90CNC - Series | Unit | PTR- 9050CNC | PTR- 9065CNC | PTR- 9080CNC | PTR- 9085CNC |
CAPACITIES | |||||
Max.turning Dia | mm | 500 | 650 | 800 | 850 |
Distance between centers | mm | 3000 | |||
Max.turning length | mm | 2800 | |||
Width of guideway | mm | 900 | |||
Max.weight of workpiece | Kg | 4000 | |||
SPINDLE | |||||
Main motor power | kw | AC22(30) | |||
Model of Spindle nose | mm | C2-11 | |||
Spindle hole | mm | 100 | |||
Taper hole of spindle | Metric 120 | ||||
Spindle taper | MT5 | ||||
spindle speeds | r/min | 10-500 | |||
Chuck | mm | 500-630mm 4-jaw manual | |||
FEED | |||||
Min.feed increment | mm | 0.001/0.001 | |||
Rapid speeds | mm/min | 3000/6000 | |||
Max.travel | mm | 330 | |||
TURRET | |||||
Turret working position | Vertical 4-position ( Horizontal 8 position optional) | ||||
Turret dimensions | mm | 280x280 | |||
Section of tool shank | mm | 40x40 | |||
TAILSTOCK | |||||
Dia. of tailstock quill | mm | 200 | |||
Travel of tailstock quill | mm | 310 | |||
Taper hole of tailstock quill | Morse5 | ||||
OTHERS | |||||
Workpiece accuracy | IT6~IT7 | ||||
Surface roughness | μm | Ra0.8 | |||
CNC Control system | SIEMENS 828D / FANUC 0i-TF |
PTR-110CNC - Series | Unit | PTR-11065CNC | PTR-11080CNC | PTR-11085CNC | PTR-110100CNC |
CAPACITIES | |||||
Max.turning Dia | mm | 650 | 800 | 850 | 1000 |
Distance between centers | mm | 3500/5000 | |||
Max.turning length | mm | 2800/4800 | |||
Width of guideway | mm | 1100 | |||
Max.weight of workpiece | Kg | 8000 | |||
SPINDLE | |||||
Main motor power | kw | AC30/AC45 | |||
Model of Spindle nose | mm | A2-15 | |||
Spindle hole | mm | 130 | |||
Taper hole of spindle | Metric 140 | ||||
Spindle taper | MT6 | ||||
spindle speeds | r/min | 8-350 | |||
Chuck | mm | 630-800mm 4-jaw manual | |||
FEED | |||||
Min.feed increment | mm | 0.001/0.001 | |||
Rapid speeds | mm/min | 3000/6000 | |||
Max.travel | mm | 450 | |||
TURRET | |||||
Turret working position | Vertical 4-position/ Horizontal 8 positions optional | ||||
Turret dimensions | mm | 300x300 | |||
Section of tool shank | mm | 40x40 | |||
TAILSTOCK | |||||
Dia. of tailstock quill | mm | 220 | |||
Travel of tailstock quill | mm | 330 | |||
Taper hole of tailstock quill | Morse6 | ||||
OTHERS | |||||
Workpiece accuracy | IT6~IT7 | ||||
Surface roughness | μm | Ra0.8 | |||
CNC Control system | SIEMENS 828D / FANUC 0i-TF |
PTR-145CNC - Series | Unit | PTR-145100CNC | PTR-145125CNC | PTR-145160CNC |
CAPACITIES | ||||
Max.turning Dia | mm | 1000 | 1250 | 1600 |
Distance between centers | mm | 5000/6000/8000 | ||
Max.turning length | mm | 4800/5800/7800 | ||
Width of guideway | mm | 1450 | ||
Max.weight of workpiece | Kg | 20000 | ||
SPINDLE | ||||
Main motor power | kw | AC75 | ||
Model of Spindle nose | mm | A2-15 | ||
Spindle hole | mm | 96 | ||
Taper hole of spindle | Metric 140 | |||
Spindle taper | MT6 | |||
spindle speeds | r/min | 5-200 | ||
Chuck | mm | 1000-1250mm 4-jaw manual | ||
FEED | ||||
Min.feed increment | mm | 0.001/0.001 | ||
Rapid speeds | mm/min | 3000/6000 | ||
Max.travel | mm | 450 | ||
TURRET | ||||
Turret working position | Vertical 4-position / Horizontal 8 position optional | |||
Turret dimensions | mm | 380x380 | ||
Section of tool shank | mm | 50x50 | ||
TAILSTOCK | ||||
Dia. of tailstock quill | mm | 300 | ||
Travel of tailstock quill | mm | 310 | ||
Taper hole of tailstock quill | Morse6 | |||
OTHERS | ||||
Workpiece accuracy | IT6~IT7 | |||
Surface roughness | μm | Ra0.8 | ||
CNC Control system | SIEMENS 828D / FANUC 0i-TF |
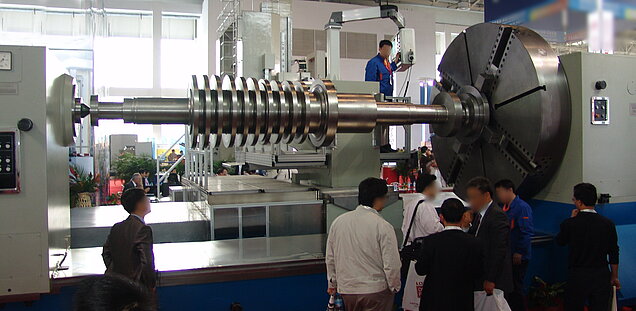
High precision heavy Duty Roll Turning Lathe
Affordable Roll Turning Machines
PTR-CNC Type Lathe is an heavy duty roll turning lathe suitable for grooving and redressing rolling rolls and cylinders. Machine is specifically designed for roll maintenance shop applications. The four guide ways are able to grant the necessary rigidity and stability for long cylinder machining. The SIEMENS (syntec, mitsubishi,..) control has full potential for demanding performance of this application. The dedicated interface makes machine operations easy and fast for machine high productivity.The main shaft bearing position very close to the faceplate (i.e. application point of radial stresses) in order to reduce the bending momentum with advantages in terms of stiffness. Large special bearings are another element that insures high performance of this component. Main gear diameter is close to the max. roll diameter to increase stiffness, decrease bending momentum and smooth high torque transmission. Guideways are ground on the heavy ribbed cast iron bed: to assure the necessary geometrical precision and a good sliding surface. No reported rail guides are used for our lathes.
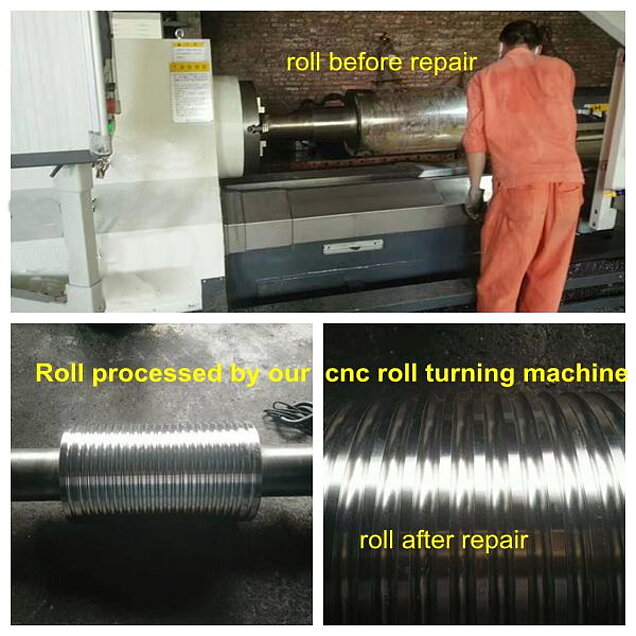
2nd Generation CNC Roll turning lathe
General PTR-CNC Series Accuracy | |
---|---|
Spindle axial channeling | ≤ 0.01 mm |
Radial run-out of spindle taper hole | ≤ 0.005 mm ( near spindle ) |
≤ 0.02 mm ( near 300 mm ) | |
Slide carriage move’s affect on spindle axis parallelism | ≤ 0.2 ( only upward bias allowed in vertical ) |
≤ 0.015 ( only forward bias allowed in horizontal ) | |
Slide carriage move’s affect on tailstock sleeve parallelism | ≤ 0.015 ( only upward bias allowed in vertical ) |
≤ 0.015 ( only forward bias allowed in horizontal ) | |
Equal altitudes of spindle and tailstock centre to centre distance | 0.02-0.06 ( only tailstock higher allowed ) |
Finish turning cylindrical precision | 0.005 mm (circular degree ) |
Fine and facing’s affect on cylindrical vertical degree | 0.02 / 300 (cylindricity) |
0.01 / 100 | |
Fine and facing’s surface roughness | Ra 0.8 |
Min. travel of vertical / horizontal | 0.001 mm |
Repeat location precision | X-axis: 0.006 |
Z-axis: 0.020 | |
Single location precision | X ≤ 0.01 mm |
Z ≤ 0.03 mm |