Centerless Grinding Basics
A centerless grinder has three main components:
a grinding wheel
a regulating wheel
a work support blade.
Because the entire workpiece is supported by the regulating wheel and the blade, centerless grinding provides a more rigid system, enabling more efficient and accurate grinding compared to grinding between centers.
If you’re trying to grind a small-diameter bar between centers, it’s very difficult because the bar wants to move and flex.
In centerless grinding, there’s no flexing because the workpiece is supported on three points.
The workpiece is rotating but not moving its position.
The grinding wheel can contain conventional abrasives or superabrasives and has a larger diameter than the regulating wheel.
Conventionally pressed wheels are produced in segments, which are joined with epoxy and/or screws and have seams that can leave markings on the length of a ground workpiece, adding also that seamless wheels eliminate any concern for that problem. In addition, manufacturing variations can exist in the sections of seamed wheels and make them prone to inconsistent wheel performance. This variation causes a wheel to breakdown at a rate consistent with its softest section.
the better and newer seamless wheels have virtually no porosity, providing consistency in the wheel from end to end and from outside to inside. In addition, compared to conventional methods that typically produce wheels with a deviation of 7 to 10 Rockwell B-scale hardness points, the seamless wheels have virtually no deviation in hardness points, resulting in very consistent wear and performance.
The seamless grinding technology extends wheel life 10 to 30 percent and enables higher stock-removal rates. Because it is stronger and tougher by nature, a seamless wheel allows you to take a heavier load on the wheel than you would typically try to take with a conventionally pressed centerless wheel.
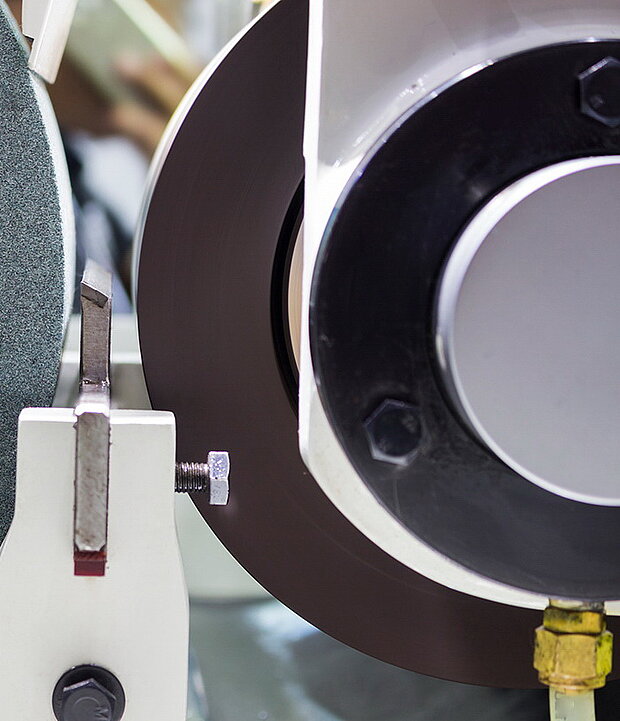
The regulating wheel, also known as a drive or feed wheel, controls the workpiece’s speed, preventing the workpiece from speeding up and rotating at the same speed as the grinding wheel. That enables the grinding wheel to remove material from the workpiece. Although a regulating wheel might have some abrasive grains in it, it is typically comprised primarily of a rubber-type bond material and doesn’t perform grinding. Other regulating wheel materials include stone and knurled steel. The regulating wheel rotates clockwise in the same direction as the grinding wheel, but at a much slower speed.
For example, a regulating wheel’s speed might be 30 rpm while the grinding wheel is rotating at 1,300 rpm. If the regulating wheel fails to do its job, you lose frictional drive from the regulating wheel, the grinding wheel takes over and the part speed will be controlled by the grinding wheel speed.
The regulating wheel angle of inclination typically is in the +1 degree to +3 degree range. This angle, along with regulating wheel speed (RPMs), determines the part thrufeed rate in mm per minute. This setting also affects the distance a part will travel in one workpiece revolution. A lower angle means a shorter travel distance and this affects grind force on the workpeice. So you can affect how a grinding wheel performs by changing regulating wheel inclination and regulating wheel RPMs. Parts that have a high diameter-to-length ratio, such as bearing rings, should have a lower regulating wheel angle of inclination to help keep the parts stable as they travel through the grind zone. Proper settings allow the workpieces to smoothly enter and exit the grind zone.
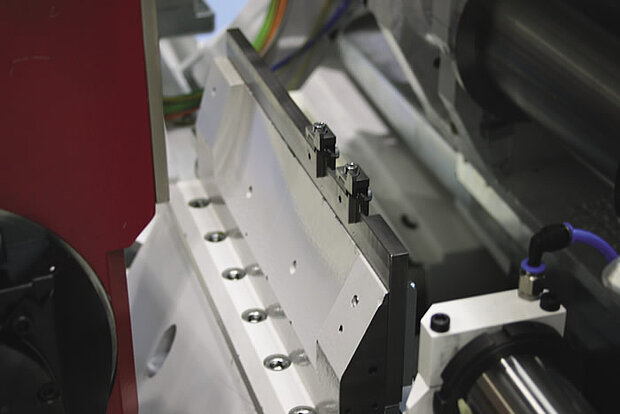
While 85 to 90 percent of the workrest blades are carbide-tipped materials, other materials, such as ceramic and bronze, are sometimes used. The blade angle varies by application—going from a flat blade for some bar grinding operations to as high as 45° for some small, intricate finishing work, but the most common angle used is 30°. The function of that blade angle is to promote roundness generation. The angle helps to not let the part drop an amount that’s equal to how much you removed from the high spots. It kind of cancels that out. The higher the angle, the faster it helps to provide roundness correction, but there are limitations.
As a workrest blade wears, a groove forms, which can cause profile problems. To prevent that, the blade is reground to the desired angle and flatness Shims can be used to adjust blade height, but other methods are available. For example, sometimes we can offer a ramp mechanism on our machines where an operator turns a setscrew to raise or lower blade height. Another alternative is a flexible slant-bed machine for quick changeover on throughfeed applications. The regulating wheel’s lower slide is set at 15°, and the upper slide is parallel to the ground. By manipulating the two slides simultaneously, the end user is able to raise or lower the regulating wheel centerline, maintaining the workpiece contact point with the regulating wheel. “For example, when going from a 45mm diameter part to a 65mm diameter part, we have the capability of changing the regulating wheel center height through the CNC rather than manually changing the rest blade height, greatly reducing one’s changeover time. This is only possible full multi axis NC/CNC machines
Infeed grinding and throughfeed grinding
A distinction is made in centerless external cylindrical grinding between two methods:
Infeed grinding:
The workpiece is inserted from the top or the side into the grinding zone and positioned by an axial stop. This is achieved by a slight inclination of the regulating wheel (0.1°–0.2°)
Throughfeed grinding:
The workpieces run continuously through the grinding zone by axial feed force. This is made possible by the inclination of the regulating wheel about its rotational axis. To ensure that, despite this inclination, all workpieces have contact across the entire wheel width, the regulating wheel has a hyperbolic shape
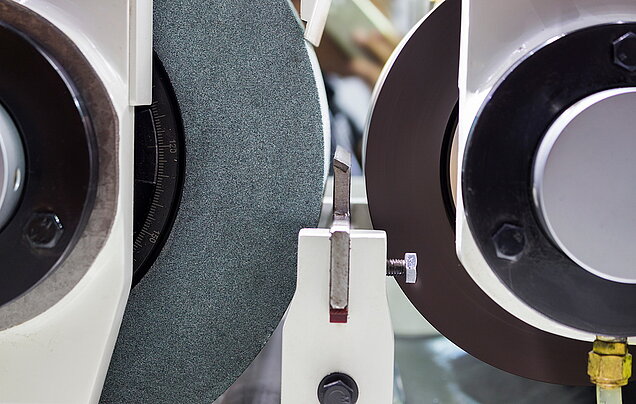
One grinding principle, three sizes – the Centerless grinding machines from Profimach offers centerless cylindrical grinding technology in the high-precision range. Centerless grinding is a special type of external cylindrical grinding, which is primarily used in the series and mass production of cylindrical components. Thanks to the linear workpiece support on the work rest and the regulating wheel, no deflection effects develop during grinding. As a result even slender workpieces can be machined on our PGCL series in excellent quality and with maximum productivity.
Spindle bearings: Rolling bearings versus Plain bearings
Normal bearing spindles versus Hydrostatic and Hydrodynamic Spindles
In the world of precision spindles, there exist two types of bearings;
rolling element bearings and non-contact type bearings.
- Rolling element bearings, as the term indicates, rotate due to integral components that roll such as balls and rollers.
- Non-contact type bearings would be defined as those that support rotation, but have no contact between the rotating and non-rotating components. Air bearings, magnetic bearings and fluid fed bearings are included. Fluid fed bearings, either hydrostatic or hydrodynamic, are integrated in high-precision spindles.
Throughout this discussion we will focus on the spindles designed to incorporate the oil fed hydrostatic or hydrodynamic bearings. Each style relies on a fluid, usually oil, to create a clearance between the moving and stationary elements. However, that is where the similarity ends. Hydrostatic bearings support a load by means of high pressure oil. Hydrodynamic bearings support a load by a lubricant film.
Journal bearings support the radial loads and thrust bearings support the axial loads. The fluid fed bearings are usually radial or axial in design. Some designs have been developed to incorporate both radial and axial functions in an opposing pair of angular or spherical bearings. Basically, the bearings float the load on a renewing film of lubricant. The hydrostatic and hydrodynamic bearing designs are substantially different from each other and are almost always application dependent.
Hydrostatic bearings require an external high pressure oil source along with a restrictor integrated into the design to provide a controlled oil film and generate load support. Generally, the oil is distributed to multiple cavities through metering devices called restrictors. Spindles built with hydrostatic bearings characteristically have high stiffness, extreme accuracy, and excellent vibration dampening features. The extreme accuracy is a result of the averaging of form errors of the surfaces that make up the bearing elements. Because a hydrostatic bearing is not dependent upon rotation to generate the oil film, it can accommodate heavy loads at zero speed. The low random motion error and vibration dampening makes the hydrostatic bearing ideal for ultra-precision machining such as those required for precision optics including mirrors.
The hydrodynamic bearing is dependent on rotation and a low pressure oil supply to build up a wedge of oil between two surfaces – the shaft and bearing – to create the oil film producing the load support. The geometry of the bearing surfaces aid in forming the wedge. A low pressure oil source is required. Spindles built with hydrodynamic bearings feature extreme accuracy, and very good vibration dampening. High loads at start-up should be avoided.
The advantages of the fluid fed bearings, as outlined, outweigh the increased costs. Spindles built with fluid fed bearings are more expensive to build. This is mainly due to low volume, the unique geometry of the bearings and the additional processing necessary to ensure the precision.
Either style of fluid bearing dictates the need for an auxiliary temperature controlled oil supply system. High pressure oil supply systems are needed for the hydrostatic bearing while low pressure oil systems are used for hydrodynamic bearings.
Because both types of fluid fed bearings are utilized in precise applications, temperature control for the oil supply system is a necessity. Oil filtration, generally in the range of 1-micron is also required. An accumulator in the oil supply system is recommended so that oil pressure can be maintained during shutdown in the event of a power failure.
When maintained as directed, spindles with fluid fed bearings can provide infinite (in theory) bearing life since there is no metal to metal contact. Failures are usually due to human error such as poor maintenance of the oil filtration, use of improper fluid viscosity, temperature control system failures, and machine crashes.
Manual centerless grinding machines Servomotor driven
Conventional Centerless Grinder
The conventional centerless grinder including gear box and servo driven type, which are electric or hydraulically controlled, represent a precise and easy way to grind small to medium sized workpieces. Features like rapid infeed, grinding feed, spark-out, rapid retraction of the handwheel to the preset grinding allowance, plus cycles for plunge and traverse grinding are included in the basic equipment.
NC centerless grinding machines
Dialogue NC Centerless Grinder - Easy HMI - Human Machine Interface
For specific, routine and big volume processing job, the NC ceneterless grinding Machine would be a very good choice.
Features:
- Easy to operate through the dialogue HMI screen.
- Reduce lost time by relying on the NC technique. When selecting 2 axes above, it can do the compensation job which precision could be below 0.002mm.
CNC centerless grinding machines
CNC Centerless Grinder
Programmable system for matching different figure and always changed workpiece or special parameters necessary during grinding.
The feeding precision of each axis is below one micron.