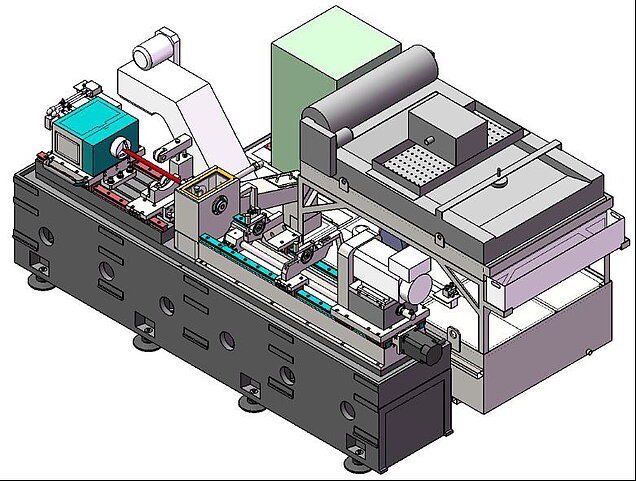
Deep hole gun drilling machines
Available in single spindle and multi spindle (2 to 6 spindles)
Profidrill pdd-series deep gundrilling
Single spindle deep hole drilling machine
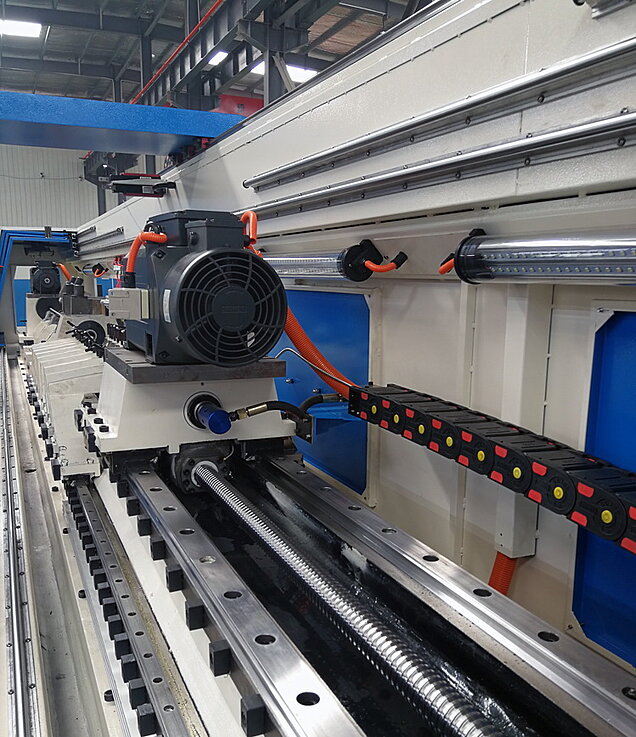
Gundrilling machines are capable of precision holes from 1 – 50 mm in diameter, and can maintain accuracy in extreme depth-to-diameter ratios.
Gundrilling uses internal coolant, and chips exit through a groove in the tool for a clean and accurate drilling process.

Gun drilling process
Gundrilling is a deep hole drilling process that uses a long, thin cutting tool to produce holes in metal at high depth-to-diameter ratios. Gun drilling is effective in diameters from 1 – 50 mm. A gundrill tool differs from a conventional twist drill by its unique head geometry; a standard gundrill has a single effective cutting edge that removes chips as it advances into a metal workpiece.
The gundrilling process is able to drill deep holes beyond what is possible with conventional machinery and tooling such as twist drills, by using high pressure coolant for clean chip exhaust, even at extreme depths.
Deep hole drilling was first developed for the manufacturing of firearms, hence the other common name of gundrilling. Originally a time-consuming and expensive process, technological advances have made it a highly efficient manufacturing process utilized in all metal cutting industries, including automotive, aircraft, aerospace, construction, medical, tool and die, petro chemical, hydraulics, pneumatics and more. Gundrilling is an ideal solution for most deep hole and high precision drilling projects. This operation produces accurate, repeatable holes with excellent surface finishes.
Gun drilling was initially developed for the manufacture of gun barrels, where both straightness and barrel durability were essential to properly functioning barrels. The gundrilling process and tooling have been refined for maximum performance and use on modern, dedicated machinery. Firearms continue to be a common application for gundrilling. Other industries include diesel fuel components, medical tooling, plastic injection molds, and more.
Gun drilling can be done, with limited performance, on common CNC machines. Holes with a depth-to-diameter ratio of 20:1 or greater generally require dedicated equipment to achieve the highest productivity and process reliability, and can reach extreme ratios of 400:1 or greater.
Gun drilling process is used to produce deep and straight holes. This process is very specialised as compared to the conventional twist drilling process. The standard gun drill tool geometry has a single effective cutting edge. Unlike the twist drill the gun drill cuts through the metal eccentrically and once inside the component the tool self-pilots itself. The hole is further burnished due to the guide pads which finally results in a precise round hole with maintained straightness.
The Coolant enters the tool through the coolant through hole and the chips are gushed out through the V shaped profile on the gun drill. Gun Drilling is effective from ф1 to ф30mm, but if you wish to go bigger in diameter, BTA drilling becomes more effective than gun drilling.
Gundrilling machines
Our gundrilling machines are ideally suited to deep hole drilling tasks with smaller drilling diameters of 2 mm to 50 mm.
A characteristic of the gundrilling method is that the coolant is introduced through channels inside the tool shaft. It is removed together with the drilling chips via a V-shaped slot (beading) along the tool. Our unique machine concept with high-quality, harmonised system components enables deep hole drilling operations to be performed down to a drilling depth of 4,500 mm or more – with maximum precision and at high speed.
Solid drilling to Ø 50 mm
Drilling depths to 3000 mm (opt 6000 mm)
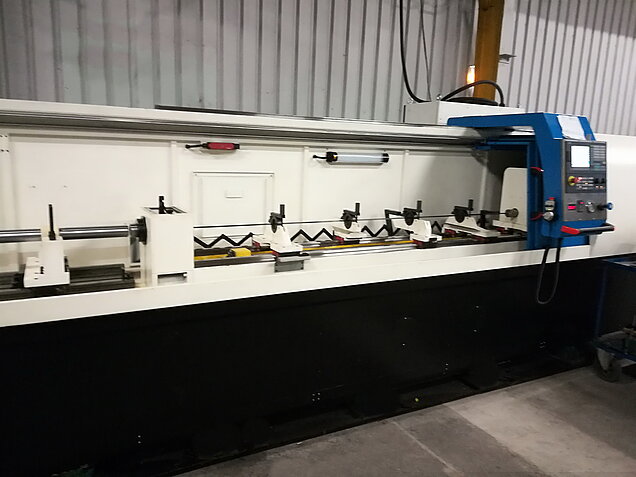
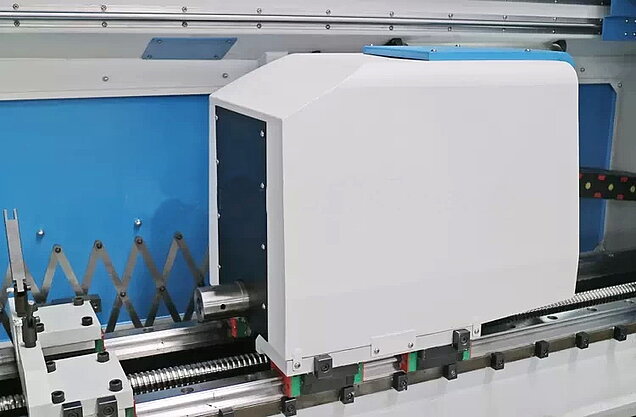
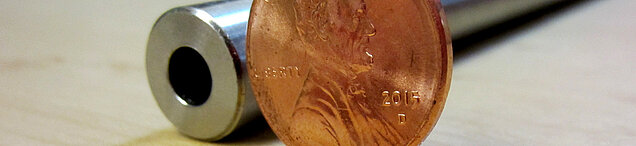