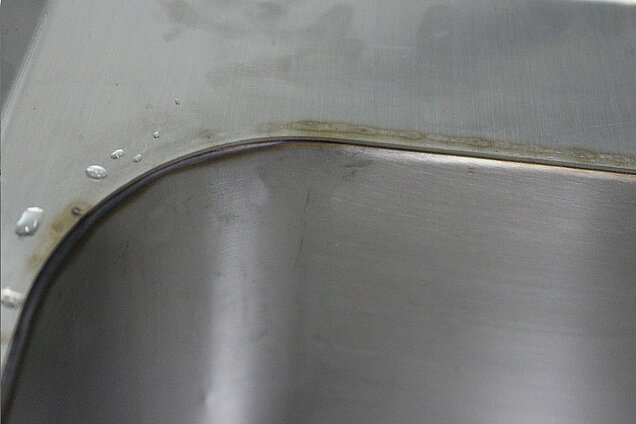
It takes less than 60 seconds to grind one stainless sink bowl.
Stainless steel sinks, which combine surfaces with bowls by welding machines, must be cleaned and grind for cleaning up the welded seams.
Our Sink top seam grinding machine is designed to grind seams between the surface and the bowls, which are welded together. The sink top grinding machine, which is equipped with a rotatable clamp, does fix the sink firmly in the rotary clamping support and grind the seam according to its shape. To grind one bowl only takes less than 1 minute. The workbench will fix all sinks tightly and rotate them with controlled speed while the grinding arm grinds the welded seams.
Comparing with manually grinding machines, this machine could assure every spot of the welded seam will be grinded with the same pressure and speed. Sinks grinded by the machine will be smoothly and brightly without any scratching. This Sink top welding seam grinding machine is very popular among sink manufactures.
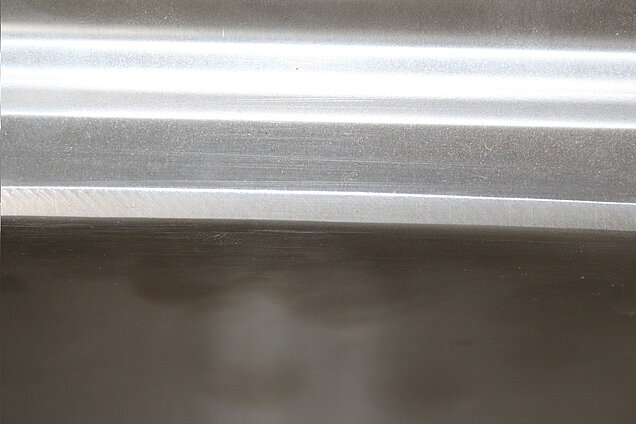
Sink Welding Seam grinding machine
Stainless steel Sink production processes
As far as the Stainless steel Sink Market is concerned, there are three kinds of processes for sink production: stamping (also called overall drawing or joint stretching), roll welding (also called bottom welding) and butt welding.
The most common in the market is the rolling welding process. This process is mainly to stretch two single slot bodies, then press a panel, weld the two slots on the panel, and then make the grinding treatment. In the process, the requirement for the drawing equipment is low, and the hydraulic equipment generally within 500 tons can be produced. However, the requirements for welding and grinding process are relatively high.
Initially, Sink producers usually adopted hand welding, manual grinding, and the combination of tank and panel is relatively rough and often has a lot of welding marks and oxide traces. More modern producers are using CNC welding and CNC grinding, eliminate the weld seams, polished very smooth and beautiful.
The advantages of roll welding process are:
1, the shape of the tank panel can be diversified, the cost of the factory production die is less (the tank die can be shared);
2, the slots panel can be made of raw material or embossing material, beautiful and generous.
3, we can make a small R slot, close to the square, and have greater use of space.
The disadvantages of roll welding are:
1. Welding process is harmful to stainless steel, easy to break the austenitic molecular structure of stainless steel and reduce corrosion resistance unless using Modern DC-DC Medium frequency weld controllers.
2. Welding and polishing technology is highly demanding, and ordinary equipment is difficult to be qualified.
3. The material waste is big and the cost is high.
The whole drawing process (also called integral stretch) is a process of directly forming one or two slots (bowls) on a piece of material through a combined die. The technological process is relatively simple, but the requirement for equipment and mold is high, and the drawing equipment needs more than 600 tons, even up to 1000 tons. In both single and double bowls, the tensile strength of the process is generally divided into two times, but the overall tensile strength needs a high temperature solution treatment in the middle of the two drawing. Solid solution treatment (also called annealing treatment) is an important process for stainless steel processing. It is a process by which austenitic stainless steel (commonly known as 304 or 316) is heated to 1050 degrees -1100 degrees and then cooled quickly.
The change of austenite molecular structure caused by stainless steel processing or high temperature welding will increase stress (too rigid) and reduce corrosion resistance. Solid solution treatment can solve this problem well, restore the material to original performance, and restore its ductility and corrosion resistance. In fact, stainless steel must be processed after cold rolling.