THRU-FEED & IN-FEED SERVO HEAVY DUTY CNC THREAD ROLLING MACHINES
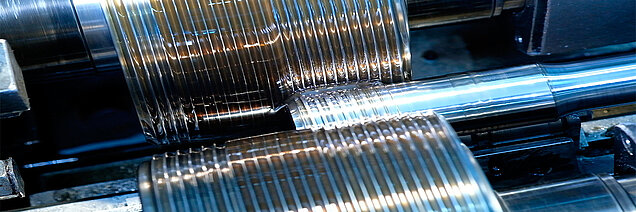
Our PTR-Pro a full CNC numerical controlled thread rolling machine with the flexibility of a CNC control system to give full control over the six axes. This development of the six axis control on the Profimach PTR-Pro is an industry first and highlights Profimach's leading role in the development of the thread rolling process. The new heavy-duty CNC machines range from 40 ton to 200 ton rolling capacity and feature a one piece bed construction that eliminates any loss of accuracy over extended rolling cycles. Control of these machines is via a CNC system that provides different programs dependent on the application. All machines in the range can be used in both in-feed and through feed applications and are available with automated part loading if required.
For many applications, thread rolling, is the best choice for creating higher quality external threads in a single pass due to it's chipless operation.
When parts are produced in larger quantities, single point threading’s versatility is less beneficial. This is because, in order to maximize effective tool life, single point inserts are processed with a limited depth of cut with multiple passes needed to cut to the thread’s full depth. The time needed to take these multiple passes can create a bottleneck. Additional passes may also be taken to deburr the thread, requiring more machine tool time or a secondary operation outside the machine. Although CNC is bringing down the total threading cycle times by making non cutting functions more efficient, these time savings are negated by the added time it takes to single point the thread. Thread rolling on the other hand, produces threads in one pass, reducing expensive CNC machining time.
In addition to doing more work on one machine in less time, thread rolling has many technical advantages over single point threading. Instead of cutting or shearing the material as is the case of single point threading, thread rolling cold forms the profile to be produced. In this process, the component material is stressed beyond its yield point, being deformed plastically, and thus permanently. A hardened die made from tool steel or HSS displaces the material along the contours of the thread profile, plastically deforming the material into the final form. The workpiece material is stressed beyond its yield point, which causes it to flow and conform to the mirror image of the die’s profile.
High benefits of Thread rolling process are:
✓ Lower costs
✓ Increased production
✓ Faster lead times
✓ Superior quality and accuracy:
○ Stronger threads
○ Improved finish
○ More accurate profile
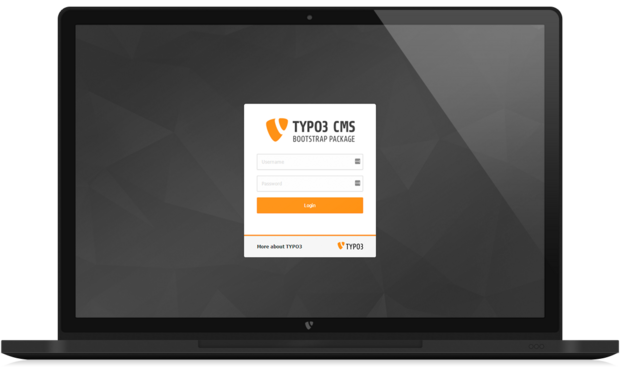