Cylinder Processing Machines
Cylinder Processing Machine for drilling out, skiving and roller burnishing of 40-400 mm in a diameter with an operating depth of max. 12000 mm
Cylinder Processing Machines are inserted today primarily in the hydraulic manufacturing, as well as in spraying mechanical engineering. Likewise, the possibility exists to use the machines with appropriate equipment also for the chamberboring of inner contours. Beyond that, the skiving and roller burnishing (tumble) used here, gains even in general mechanical engineering more and more significance. For example, construction units with high surface quality which require at the same time a high standard of firmness by solidification of the workpiece surface. Cylinder Processing Machines can be used beside the usual drilling out skiving and roller burnishing operations also for full boring, depending on installed achievement and equipment. Here, fast re-equipping particularly becomes effective by a sensible building block principle, so that secondary times are reduced to a minimum. For drilling and/or peeling and smooth rolling mill tool, all commercial tools can be used.
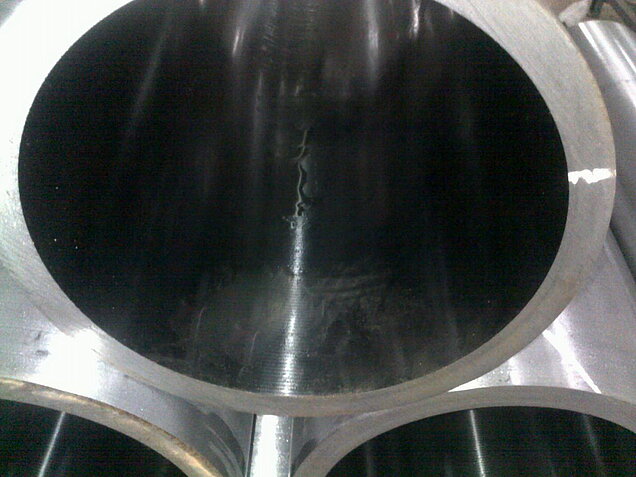
Deep hole skiving roller and burnishing machine
Deep hole skiving roller and burnishing machine is a new type of efficient deep hole machine, independently developed by our company reference to the technology of the similar foreign machines. Deep hole skiving roller and burnishing machine is equipped with large power, strong rigidity, wide margin of machining process and extremely high machining efficiency, is the ideal equipment for all kinds of cylindrical workpieces with deep holes. Deep hole skiving roller and burnishing machine can process a variety of mechanical hydraulic oil cylinder, cylindrical workpiece holes and ladder holes, etc.
Deep hole skiving roller and burnishing machine is mainly used for boring and rolling processing, machine tool adopting the precision boring cutter rotating scrape, rolling processing technology. Remove chips in front when boring and scraping and the boring way is to push boring, granted by the oil tank in central of boring bar, remove chips on the head of a bed. The rolling is the post-tensioning, applies the high-speed scraping and boring rolling head, can processing efficiently the oil cylinder, reversing the traditional process of a rough boring, glossy boring, grinding cylinder, the production efficiency is the traditional process of 5 to 10 times. Application of this machine will have an epoch-making revolution for the oil cylinder production. Cylindricity and alignment of processing workpieces is very high, cutting and rolling speed can reach 1 m/min with the cylinder produced by cold drawn pipe, cutting and rolling speed can reach 0.3 m/min with the cylinder produced by hot rolled pipe. Finish the molding at the first time.
The bed of deep hole skiving roller and burnishing machine is manufactured by high quality cast iron, with strong rigidity and strong stability. Boring bar box spindle is drove by ac servo motor, boring bar box spindle is drove by servo motor, wide speed range, large output torque, feed system uses AC servo motor driven double rack transmission, smooth feeding, long service life and can adapt to the needs of all kinds of deep hole machining process, workpiece loading card adopts tight hydraulic cylinder, stable and reliable, easy handling, electrical system adopts centralized control CNC system, can be interactive, graphical display, flexible operation, safeand reliable. In production it is suitable for mass production can also be suitable for small batch production.
Deep hole skiving roller and burnishing machine is equipped with large capacity automatic chip removal machine, drum magnetic separator, collect automatically iron into attle box, cooling fluid can be recycled by precision filtration.
The accuracy of SRB machine machining
Precision of bore diameter: drilling hole IT8 ~ IT9; Boring hole IT7
Roundness: 0.036mm/Ф200mm (after the fine boring)
Cylindricity: 0.05/500mm (after the fine boring) 40mm-1200mm (different model)
Roughness:
Heavy boring Ra 6.3µm
Fine boring Ra 1.6µm
Rolling: Ra 0.4µm
More information on Tube Skiving Roller Burnishing Machines Machines: Click Here
www.deepholemachines.com
www.deepholemachines.com
Website fully dedicated to Tube skiving and roller burnishing and deep hole drilling
Before and after SRB - Skiving & Roller Burnishing
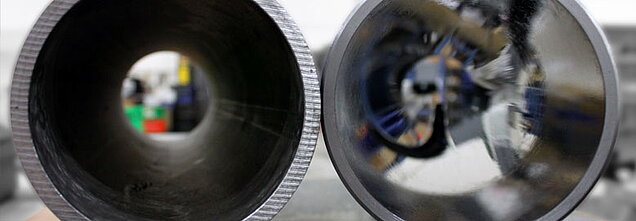
Skive Burnishing Tool Operation
Skiving in, Rolling out.
Skiving operation: Two thin chips are cut at a high feed rate of 1-4 mm/rev (0.04-0.16 inches/rev) while the tool passes through the workpiece. This cutting operation determines the finished diameter and tolerance of the cylinder. Surface finish Ra= 4-10 μm (skiving).
Roller burnishing operation: Roller burnishing is performed on the return stroke. The plastic deformation taking place provides a surface finish of Ra= 0.05-0.20 μm – better than broaching, grinding or even honing. Localized surface hardness is increased by approximately 50% (steel).
Skiving in, Rolling out.
Skive burnishing tool combines two machining processes into one seamless operation. On the initial stroke, the skiving tool, which operates as a ‘floating reamer’, utilizes supported carbide inserts to slice away chips and produce a geometrically round bore – an ideal pre-finish for roller burnishing. On the return stroke, connected air pressure forces the inserts on the skiving head to retract, allowing the multi-roll burnishing tool to engage and compress any residual peaks.
This process is the fastest method for producing mirror-like finishes to inside diameters of cylinders, benefitting from; a tough work-hardened surface, improved fatigue life and introducing a residual stress layer to the internal wall. This makes the burnished surface the preferred choice for manufacturers of pneumatic and hydraulic cylinders with seamless or Drawn over Mandrel (DOM) tubing – offering typical savings of 80-90% compared to honing.
The tool produces a superior surface finish as fine as Ra= 0.05-0.20 μm with a bore tolerance of IT8, and localized work hardness of up to 50%, thereby reducing the sealing wear making it ideal for pistons.
Standard skive burnishing tools are designed as ‘dual-pass’ so that the tool parameters can be optimized for both the skiving and roller burnishing – allowing power and feed force to be kept to a minimum and ensuring that the part is not damaged when retracting the tool. The tools can be used in a rotating, non-rotating or both rotating configuration as required.
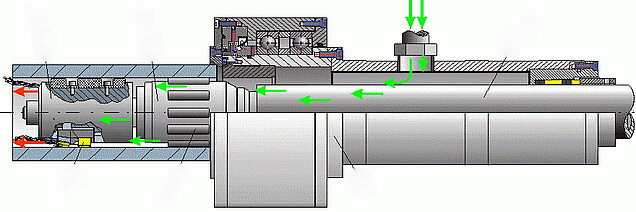
Skive and Roller Burnishing is a modern process to rapidly finishing the interior diameter (ID) of a tube to a cylinder quality size and finish.
Skive and Roller Burnishing is a modern process to rapidly finishing the interior diameter (ID) of a tube to a cylinder quality size and finish. A Skive and Roller burnishing tool uses a floating carbide cutter that produces a true round bore in the Skive operation and a work hardened seal friendly surface in the Roll operation.
Skiving in itself is a process used to remove stock where close tolerances and roundness are required. Skiving produces a surface finish of approximately 1,5 – 3,2 micron center line average (CLA). The depth of cut can range from as little as 0,3 mm per side and as much as 12 mm per side depending on the size of the tool. However best results come from material produced specifically for Skiving. Skiving also produces optimal peak and valley patterns for subsequent roller burnishing.
A Skived tube will have a tighter tolerance than available through DOM or Seamless tubing products. A Skived Only condition can be used to reduce costs by leaving minimal stock to clean up the ID after a weld operation or when a Skive and Rolled finish is not desired. It can also be used to remove excess stock quickly and efficiently.
Roller Burnishing can follow the Skive operation. This operation employs rollers which causes material to flow from the "peaks" into the "valleys". The burnishing process produces a more condensed and refined surface finish which reduces seal friction and surface porosity. A surface finish of 12 Ra or better is common.
Skived Only Advantages:
1. Faster processing than conventional rough or swipe honing.
2. Reduced roughing costs.
3. Reduced finishing stock after welding.
4. Reduced stock removal for finish honing.
5, consistent size end for end.
Skive and Roller Burnishing Advantages:
1. Faster processing than finish honing operation
2. Reduced finishing costs.
3. Harder surface finish by up to 10 points HRC.
4. Work harder wear surface improves seal life.
5. Improved corrosion resistance.
6. Consistent size end for end.
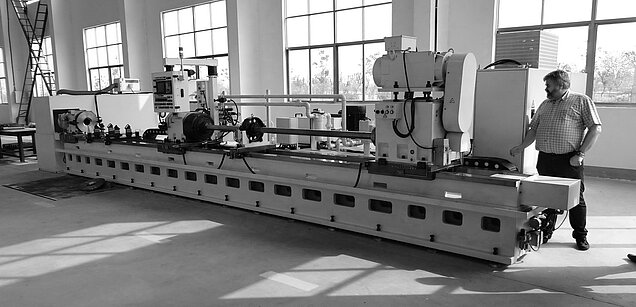
Benefits of skive burnishing over honing
-
80-90% reduction in machining time
-
Reduced tool costs per metre (foot) of tube length
-
Produces an even, mirror-like finish ideal for pistons – reducing sealing wear
-
Superior surface finish – down to 0.05-0.20 μm
-
Improved size control – bore tolerance of IT8 or better may be achieved
-
Improved cylinder fatigue life – up to 300%
-
Localized work hardness – up to 50%
-
Introduction of a residual stress layer to the cylinder wall
-
Enhanced corrosion resistance
-
Cleaner than honing or other abrasive operations
SRB - Skiving Roller Burnishing
Controlled roughness, roundness and straightness
SRB operation ( Skiving Roller Burnishing) is distinguished compared to traditional solutions of honing and roll burnishing due to internal finish that provides:
- Improving of inside walls generatrix equaldistance, with reference to the rectilinear tube axle.
- Inside Straightness, better than 1/1000 of the tube length towards the original one of the mother tube.
- Controlled Roughness to ensure the seal has auto lubrication on a finished surface having only troughs (no peaks) and full steel planarity at 1 MY Max Depth bearing ratio.
- Extreme surface cleaning, absence of metal micro-particles compared to traditional honing and roll burnishing
-
Through our inside finishing production process we achieve an RA profile characterized by exclusively negative micro picks, these are generating small oil pockets in the surface, improving the system lubrication allowing an optimal bearing surface to improve seal life for a longer period.
-
Furthermore our production process gives a better performance on inside straightness against the maximum tolerances allowed by the norms and the profile bearing goes over 50% at 1 my depth.
Combined Skiving and Roller Burnishing
The combination of machining (skiving) and a transforming process (roller burnishing) is an extremely efficient method for finishing of pipes. For the use of hydraulic cylinders, there are special requirements for roughness and forming tolerance. At the same time it must be superior to competing techniques, such as honing. The combination of skiving and roller burnishing does meet these requirements.
The machining takes place in the anterior part of the tool on three or six floating knives, which are supported on a common center. This arrangement ensures a very good circle. The chips produced during machining are flushed out to the front of the tube, because after the machining the roller burnishing process takes place. The resulting surface has Ra values of about 0.2 microns or less. This requires no further editing. Such combination tools can be used with diameters of 38 to 650 mm and lengths of pipe up to 18 m. The latest generation of these tools also has an attachable boringhead. So the triple processing is possible for simultaneous counter boring, skiving and roller burnishing
More information on Tube Skiving Roller Burnishing Machines Machines: Click Here
www.deepholemachines.com
www.deepholemachines.com
Website fully dedicated to Tube skiving and roller burnishing and deep hole drilling
SRB machine major construction specifications
For a hydraulic cylinder to operate effectively, the cylinder’s ID must be precisely round and have a mirror-like surface finish to ensure a tight seal between it and the mating internal piston. This is commonly achieved through skiving and subsequent roller burnishing inside a tubular workpiece. Skiving uses a set of carbide blades positioned around the diameter of a tool to slice away chips and create a geometrically round bore. Roller burnishing, a cold-working process, uses multiple rollers to compress the peaks of material left behind after skiving to generate an extremely smooth surface finish. Burnishing also introduces a residual stress layer into the cylinder wall, which improves cylinder fatigue life.
These operations are sometimes performed in one pass using a combination skiving/roller burnishing tool on a BTA-style deep-hole drilling machine. However, Profimach , has designed machines engineered specifically to perform skiving and roller burnishing operations, noting increasing demand in the hydraulics market for such equipment. Its SRB-series machines use a single tool for both operations, achieving roundness tolerances of IT-8 or IT-9 and bore surface finishes as smooth as Ra 0.05 to 0.2 micron in one setup and one tool pass.
Where others have 80 percent of the SRB-series machine design is based on their existing BTA-series, we fully developped a complete machine uniquely designed for a perfect SRB job. A real Skiving roller Burnishing machine optimazed for the production of hydraulic cylinder tubes.
Three distinct features that enable the SRB-series to be highly effective at skiving and roller burnishing:
• Workholding
The tubes used for hydraulic cylinders are relatively thin. Care must be taken to secure the tube rigidly enough for the skiving and roller burnishing processes, but not so tightly as to deform it. Therefore, clamping cones are typically used to hold the tubes on both ends instead of three-jaw chucks. This clamping method also facilitates quick workpiece changeovers in automated environments. In addition, extra support must be provided along the length of the tube due to the inherently high length-to-diameter ratio of these workpieces. The SRB-series uses a V-shaped hydraulic clamp to provide this support.
• Power train
Thin cuts are taken during skiving. A skiving blade’s radial engagement with the workpiece might be just 3 mm and feeds might be 1 mm per revolution, per blade. However, each tool has two/four or three/six skiving blades, which multiples the effective feed rate. Similarly, the cold-working roller burnishing process requires a lot of torque and high spindle speed as it plasticizes and compresses the peaks that skiving leaves behind. As a result, the SRB-series features a more robust power train with higher horsepower motors and faster spindle speeds than conventional BTA drilling machines.
• Rotary union
A hydraulic circuit inside the skiving and roller burnishing tool expands the skiving blades and burnishing rollers during cutting operations. Therefore, the SRB-series has a rotary union at one end of the tool headstock to provide a hydraulic connection throughout the length of the rotating tool. Once the cutting pass is completed, the blades and rollers are retracted into the tool as it is removed from the tube. The tool continues to rotate as it is removed, but nylon guides on the tool and continuous coolant delivery prevent damage to the cylinder wall.
The SRB-series machines are available in skiving/burnishing diameters ranging from 35mm to 850mm and lengths to 18 m (larger machines are available upon request). The machines can also be modified to perform besides SRB also BTA drilling, counter-boring, and other drilling and tube-finishing operations. In addition, tools can be configured to perform tube finishing on a variety of metals.
Click here if you want MUCH more information on our deep hole working machines
www.deepholemachines.com
Skiving roller burnishing, skiving and roller burnishing, skiving burnishing, roller burnishing, skiving and roller burnishing machine, skiving burnishing machine, skiving roller burnishing machine, skiving roller burnishing machines, skiving and roller burnishing machines, skiving burnishing machines, skiving & burnishing, skiving & burnishing machines, cnc skiving and roller burnishing machines, cnc skiving roller burnishing machines, cnc skiving burnishing machines, SRB machine, SRB machines, cnc srb machine, skiving, skiving machine, cnc skiving machine, roller burnishing, roller burnishing machine, burnishing, combined skive-burnishing, CNC deep hole skiving roller burnishing machine, Skiving & Burnishing Machine, Skiving/Roller burnishing, skiving-roller-burnishing, Machine combines skiving and roller burnishing, Cylinder Processing Machines