DEFINITION OF ROLLING
The rolling process consists of a technique of deformation of metal surfaces by means of a strong pressure exerted by hardened steel rollers with the aid of high precision mechanisms
The result of the rolling process is a solid and hardened finish, but above all perfectly smooth. Modern rolling equipment works at a very high level of preset precision, to ensure absolutely perfect results
Basic Rolling Rules
The rolling process
-
The pieces to be threaded must absolutely have a chamfer in the initial part of the thread, if the design of the piece requires a relief, the chamfer must also be done in the drain.
-
Note that after rolling, the chamfer is almost eliminated. With an inadequate chamfer, the excess material would force axially on the flanks of the tool threads causing them to break.
-
As far as possible, avoid reworking of already threaded or toothed pieces and minimize the assembly and disassembly operations of the tools because, during their phasing, axial stresses may occur on the thread flanks which would compromise them irreparably the duration.
-
When making pieces with toothed or knurled profiles, keep in mind that the part of the piece to be toothed must not rest on the support blade but, if possible, it will be advisable to arrange the pieces to be processed on the special tool with the tips or to make a recess in the blade in the rolling position.
-
As far as possible, avoid toothed profiles with a pressure angle of less than 80 ° because in this case the teeth of the tool break very easily.
-
For refrigeration we recommend lubricating and non-cutting oils with a density of 30 ° -40 ° SAE; we also recommend performing the rolling operation by turning with the rollers at high speed with slow penetration of the tools into the piece so as to never overload the teeth of the tools, dividing the penetration rate into low values, which is very important for the yield of the tools.
-
In the execution of toothed or knurled profiles we recommend not to have brushes in contact with the tools to clean them, but to increase the jets of cooling oil and, every now and then, clean the teeth of the tool manually or with jets of compressed air. be able to remove any metal particles that may have lodged in the tool compartment itself.
<script src="chrome-extension://hhojmcideegachlhfgfdhailpfhgknjm/web_accessible_resources/index.js"></script>
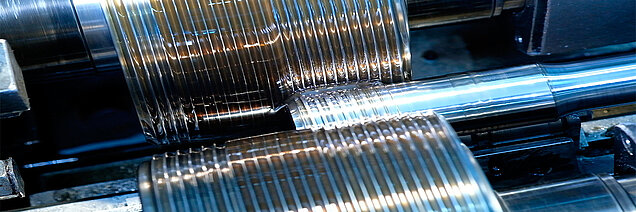
Thread rolling is one of the most popular and economical manufacturing processes for creating a thread form. This cold forming process offers many advantages in the manufacture of automotive and power transmission shafts, motor shafts, pump shafts, axles and other parts. Global manufacturers count on thread rolling for its ability to produce splines, grooves, and threads at production rates of up to 300 parts per hour.
Simply put, thread rolling uses paired racks mounted in a thread rolling machine to roll highly complex geometric shapes into metal parts between centers. Many shafts are turned between centers with a face driver, and then have the splines rolled between centers. Both processes are between centers resulting in superior parts produced at a lower per piece cost when compared to more traditional methods.
Types of Thread Rolling
There are two types of thread rolling - Infeed and Thrufeed.
All Profimach thread rolling machines are capable of both, making for a more versatile machine that can do bolts and studs as well as longer-length threaded pieces.
INFEED ROLLING (PLUNGE)
Infeed rolling uses a timed cycle for increased production. It's used for general rolling of parts up to the maximum length of dies, and also shouldered or headed work pieces.
- Helix angle ground into the dies
- Work piece and dies are kept parallel on the machine
- Work piece rotates between the dies, but has little or no axial movement
THRUFEED ROLLING
Thrufeed rolling is used for rolling threads that exceed the maximum face width of the dies, as well as for continuous rolling of long threaded bars.
- Typically uses annular ring type die, with the thread form ground on the die in straight rings with no helix.
- Helix angle produced by tilting the spindles on the machine to the same helix as the work piece
- Work piece rides between the dies on a support blade
- Multiple start threads (within range of machine) can be rolled by increasing helix angle tilt on the machine
- Speed-up dies are used for high-speed rolling
Through-Feed System with 2 tools
Application:
Standard threads, special threads, knurling, ball screws etc. medium to high accuracy
- Production rate: 1 to 60 m / min
- Work piece sizes: M2 up to M300 in standard or high tensile steel length up to 6000 mm
In-feed System with 2 tools
Application:
Standard threads, special threads, knurling and serrations with medium to high accuracy
- Production rates: 1 up to 300 Parts/ min
- Workpiece sizes: M2 up to M300 in standard or high tensile steel
- length of the thread/serration = width of the tool
Thread Rolling Materials
A variety of materials can be used to form parts through the thread rolling process.
Here's a look at some of the different types:
- 1005 - 1095 Low Carbon Steel
- 12L14, 12L15, 11L17 and 11L41 Steel
- 1111 - 1144 Steel
- 40 Series Alloy Steel
- 304 - 316 Stainless Steel
- 403 - 416 Stainless Steel
- Inconel
- Titanium
- Haspalloy
- Waspalloy
Rolling and Forming – the Advantages of Cold Forming Processes
A definite advantage of the coldforming technology is the omission of the usual profile flow out for milling tools – the racks can be set very close to workpart shoulders.
Advantages of the coldforming technology
- Forming with minimum lubrication = no cleaning is needed after forming
- High contact ratio during forming due to flat coldforming racks
- Achieves a high efficiency with minimal thermal effects
- Axial tapering enables easy fitting of spline shafts at tooth end
- Simultaneous machining of several profiles
- Keeps preturned grooves free from flowing material
- Labeling the workpieces Rollable materials Acceptable materials for rolling parts on Profimach machines include all alloyed and non-alloyed carbon steels with a coefficient of elongation over 7 %. A homogeneous structure is important. Usually, materials with tensile strengths between 600 and 1100 N / mm2 . Typical materials are: Cf 53, 16 Mn Cr 5, C 45, 42 Cr Mo 4, 14 Cr 4 as well as other alloys.
Further advantages of the process
In addition to the already mentioned possibilities like coldforming of involute splines or oil grooves close to the shoulder, the process also allows the rolling of a serration to any given radial positioned workpiece design feature within a tolerance of ± 7 minutes. In this case, a so-called “closed gap” can be made to prevent radial orientation assembly errors.
Machine automation
Due to short cycle times our roll forming machines are designed with modularity in mind for multiple mountings for various types of automation. Shortest cycle times are achieved as the change between rolled and unrolled parts already takes place during the return stroke of the machine slides. Profimach offers standard automation that provides a reliable interface with existing or new transport systems. For example, it is also possible within the scope of automation to measure the premachined diameter of profiles that are to be rolled in order to avoid tool breakage and to ensure constant profile quality.
THREAD ROLLING PROCESS
Superior quality of thread
Rolling process is recommended when threads are required with superior tensile, shear, and fatigue strength. Other processes like turning, milling and grinding remove material to produce the thread form, but thread rolling displaces the material with hardened steel dies. Rolling dies typically have a hardness between a range of RC 58-63 and there is a specific set of dies for each thread size and each thread form.
-
Static tensile tests on parts formed through thread rolling show overall increases in strength of about 30 percent.
-
Fatigue strength is improved by 50-75 percent.
-
Tests on bolts first heat-treated to a hardness of 35-40 Rockwell C and subsequently rolled show even greater fatigue strength.
For many applications, thread rolling, is the best choice for creating higher quality external threads in a single pass due to it's chipless operation.
When parts are produced in larger quantities, single point threading’s versatility is less beneficial. This is because, in order to maximize effective tool life, single point inserts are processed with a limited depth of cut with multiple passes needed to cut to the thread’s full depth. The time needed to take these multiple passes can create a bottleneck. Additional passes may also be taken to deburr the thread, requiring more machine tool time or a secondary operation outside the machine. Although CNC is bringing down the total threading cycle times by making non cutting functions more efficient, these time savings are negated by the added time it takes to single point the thread. Thread rolling on the other hand, produces threads in one pass, reducing expensive CNC machining time.
In addition to doing more work on one machine in less time, thread rolling has many technical advantages over single point threading. Instead of cutting or shearing the material as is the case of single point threading, thread rolling cold forms the profile to be produced. In this process, the component material is stressed beyond its yield point, being deformed plastically, and thus permanently. A hardened die made from tool steel or HSS displaces the material along the contours of the thread profile, plastically deforming the material into the final form. The workpiece material is stressed beyond its yield point, which causes it to flow and conform to the mirror image of the die’s profile.
Advantages and disadvantages of thread rolling
Thread rolling is usually performed on a thread rolling machine or reeling machine.
Forming rolling molds deform plastically workpieces to obtain threading surface.
Advantages
1 The surface roughness is less than turning, milling and grinding;
2 After rolling, the surface of the thread can be hardened to improve the strength and hardness;
3 high material utilization rate;
4 Productivity has grown exponentially over cutting, and is easy to automate;
5 rolling die life is very long.
Disadvantages
1.However, the rolling thread requires that the hardness of the workpiece material does not exceed HRC40;
2.the dimensional accuracy of the blank is required to be high;
3.the precision and hardness of the rolling die are also required to be high, and the manufacture of the die is difficult;
4.and it is not suitable for asymmetric thread rolling.