PROFIMACH PG-CBC-40-Series
Automatic Carbide Blanks cutting production redefined!
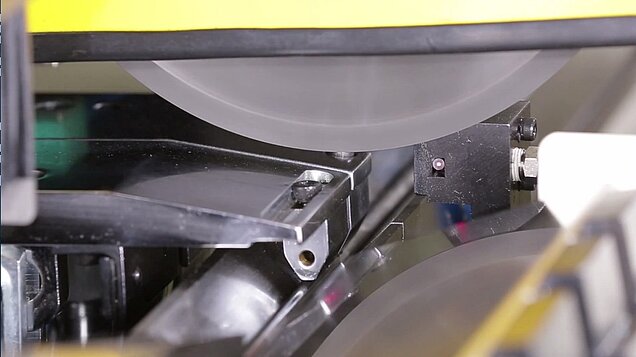
PROFIMACH PG-CBC-40-Series
Automatic Carbide Blanks cutting production redefined!
Profimach® PG-CBC-40-series. This new range of premium Carbide Blank Cutter sets standards in his category. Its values are simplicity, modernity, innovation and robustness allied with a never seen price/performance ratio.
The machine design, optimized by means of state of the art simulation and analysis tools provide solidity throughout the machine. The result is a stable grinding behavior which ensures a lasting quality of a high accuracy production process.
The perfect harmonization of both machining performances and stability is the fruit of innovation efforts based on the long experience of our engineers. The result is reliable high precision production equipment with an irreproachable operation in any situation.
The generous standard equipment underlines the versatility of this concept of the latest generation.
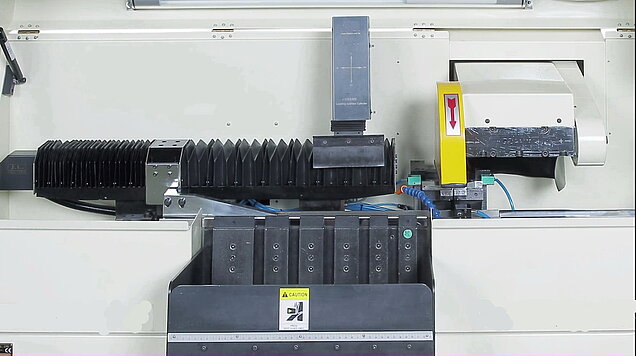
The design of the guards allows for optimum viewing of the part being machined.
Totally enclosed guarding includes roof top/side to keep all the chips, water and noise inside the machine and to have clean, quiet and comfortable environment also around the machine.
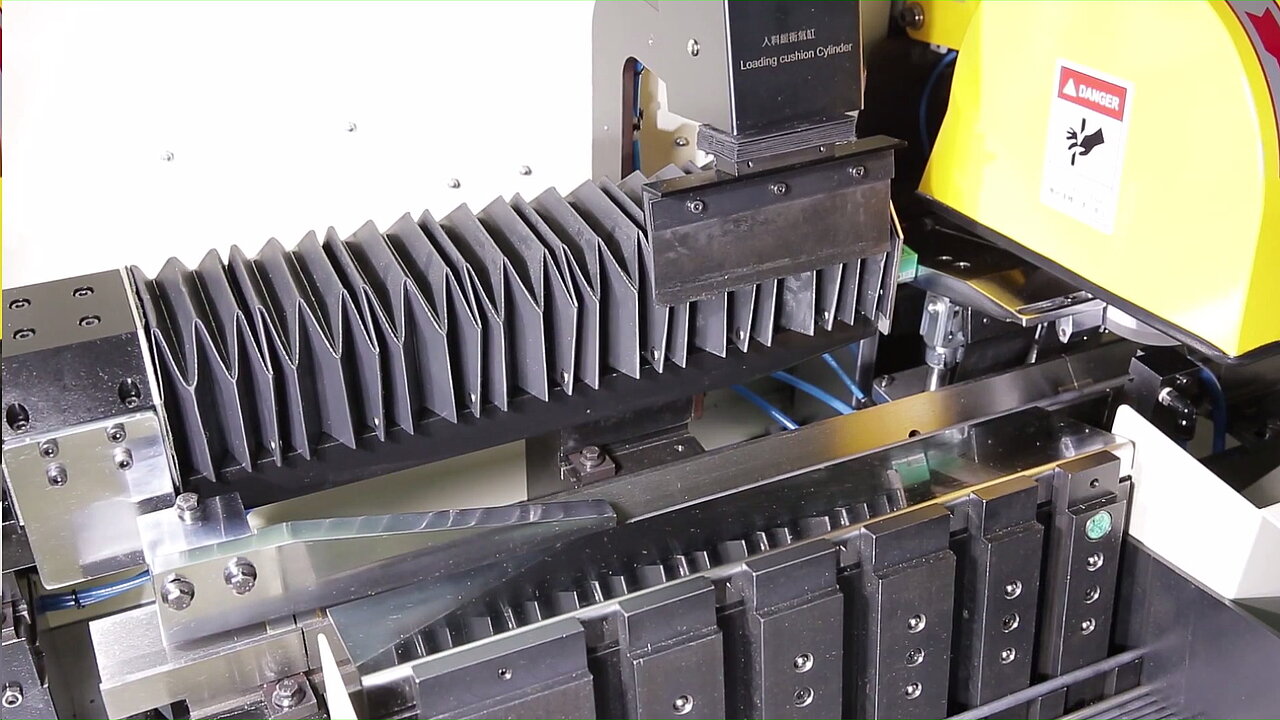
PROFIMACH PG-CBC-40-Series
Optimized to perfection
Function Specification | One piece a time | Two pieces a time |
---|---|---|
Range for out Dicmeter | Ø 1.4 ~ 35 | Ø 1.5 ~ 21 |
Range for Length | 100 ~ 420 | 100 ~ 420 |
- Able to load diameter from Ø2 mm to max Ø40 mm
- loading length max 400 mm
- Cutting length from 5 mm to 350 mm
- Machine: Length 2030mm Width 1100mm Height 1960mm /
- Net Weight: 985kg
USAGES AND FEATURES LISTED AS BELOW:
1. ABLE TO LOAD DIAMETER FROM Ø2 MM TO MAX Ø40 MM, LENGTH MAX 400 MM
2. SUPPORT TO CUT OFF TWO BARS A TIME
3. CUTTING LENGTH FROM 5 MM TO 350 MM
4. APPLY TO CUT OFF SOLID CARBIDE TUNGSTEN ROD OR HSS ROD
5. TOUCH SCREEN AND USER-FRIENDLY PROGRAM SETTING TO INCREASE PRODUCTION
EFFICIENCY AND SAVE SETUP TIME AS WELL AS MAN POWER.
6. PROGRAM SELF-CALCULATED FUNCTION, CAN POWER OFF AUTOMATICALLY AFTER
OPERATION STOP A WHILE.
7. POWER OFF AUTOMATICALLY WHEN REPLACING THE WHEEL FOR USER SAFETY
8. MIC-300A-26 ELECTRIC LUBRICATION INJECTOR & BELLOWS COVER TO KEEP THE LIFE
OF BALL SCREW AND PREVENT THE CARBIDE POWDER STICK INSIDE
9. MACHINE IS EQUIPPED WITH LUMINOUS LAMP AND RESERVE A HOLE FOR OIL MIST
COLLECTOR CONNECTION.
10. CUTTING SPEED THREE SECTION CAN SET UP FOR TINY SPEED CONTROL
11. PROGRAM CAN BE UPDATED BY THE USER TO KEEP THE LATEST PROGRAM VERSION
12. HOLDING SET OF V TRAY AND BALL SCREW ADJUSTABLE FOR BETTER AFTER CUT
SURFACE.
13. CUTTING LENGTH TOLERANCE: +-0.05MM
USER-FRIENDLY & ERGONOMIC GUARDING DESIGN : The machine design, optimized by means of state of the art simulation and analysis tools provide solidity throughout the machine. The result is a stable grinding behavior which ensures a lasting quality of a high accuracy production process.
The design of the guards allows for optimum viewing of the part being machined. Totally enclosed guarding includes roof top/side to keep all the chips, water and noise inside the machine and to have clean, quiet and comfortable environment also around the machine. The machine has been carefully designed to provide a reduction of overall floor space dimensions.
Standard equipment:
1. Diamond Cut-off Wheel (1pc) :Thickness 1mm OD 200mm IH19.05mm
2. Wheel motor of cutting spindle is imported from Europe, 4P 5.5HP 623B3
3. Σ-ⅤAmplifier 400W Σ-ⅤServo motor 400W (Cutting length control)
4. Σ-ⅤAmplifer 400W Σ-ⅤServo motor 400W (Cutting speed )(Saw up/down)+ VGM Decelerator MF60XL1-4-K-14-50
5.Controlling system: Motion controller MICRO(UTC-400V+) (Conversational interface)/UT-760 7'' color touch screen /Hand wheel IHDW-AA-80
6. Festo Pneumatic Unit (10 T-terminal Solenoid valve/Regulator/F.R.L Unit /Cylinder …)
7. THK KR3310A-600L Ball screw (Linear mdd combination) (Feeding& cutting length)
8. Coolant tank with pump (1 unit) Size L500 W 500 H520(mm) /Tool box(1 Set)
9. This quotation doesn't include the oil mist collector & coolant filteringsystem
The 2 Rod “Auto-Cut” CNC Carbide Cut-Off Machine automatically cuts carbide rod into precision lengths. This production machine, designed for cutting tool
manufacturers and carbide rod processors, has a large capacity magazine and an automatic loader to provide hours of unattended operation.
The 2 Rod “Auto-Cut” can quadruple the production rate for cutting carbide and hardened steel rod when compared with manual cut-off machines. It has easy to use NC/CNC controls with a touch screen operator interface. Parameters can be quickly set for rod diameter and length. The machine automatically loads and cuts rods from a large capacity magazine.
Capacity of the 2 Rod “Auto-Cut” is 2 mm to 20 mm diameter rod, up to 400 mm long, and comes standard with a flood coolant system.”
The “Auto-Cut” NC Carbide Cut-Off Machine
The “Auto-Cut” NC/CNC Carbide Cut-Off Machine automatically cuts carbide rod into precision lengths. This production machine, designed for cutting tool manufacturers and carbide rod processors, has a large capacity magazine and an automatic loader to allow for hours of unattended operation.
The “Auto-Cut” can double the production rate for cutting carbide and hardened steel rod when compared with manual cut-off machines. It has easy to use CNC controls with a touch screen operator interface. Parameters can be quickly set for rod diameter and length. The machine automatically loads and cuts rods from a large capacity magazine.
Capacity of the “Auto-Cut” is 1.4 mm to 40 mm diameter rod, length capacity 80 mm to 420 mm, and comes standard with a flood coolant system.
Premium Carbide Blank Cutter
This new range of premium Carbide Blank Cutter sets standards in his category.
Its values are simplicity, modernity, innovation and robustness allied with a never seen price/performance ratio.
The machine design, optimized by means of state of the art simulation and analysis tools provide solidity throughout the machine. The result is a stable grinding behavior which ensures a lasting quality of a high accuracy production process.
The perfect harmonization of both machining performances and stability is the fruit of innovation efforts based on the long experience of our engineers. The result is reliable high precision production equipment with an irreproachable operation in any situation.
The generous standard equipment underlines the versatility of this concept of the latest generation.
Cutting Carbide rod with different diameter
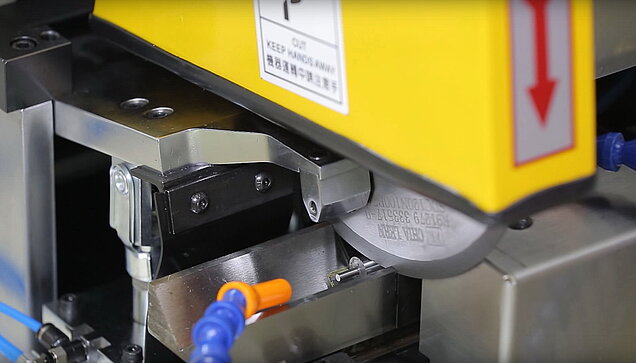
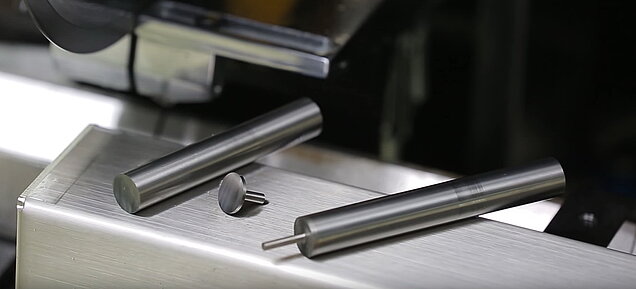