Profimach Centerhole grinding machines
PGCH-125M - - - PGCH-185M
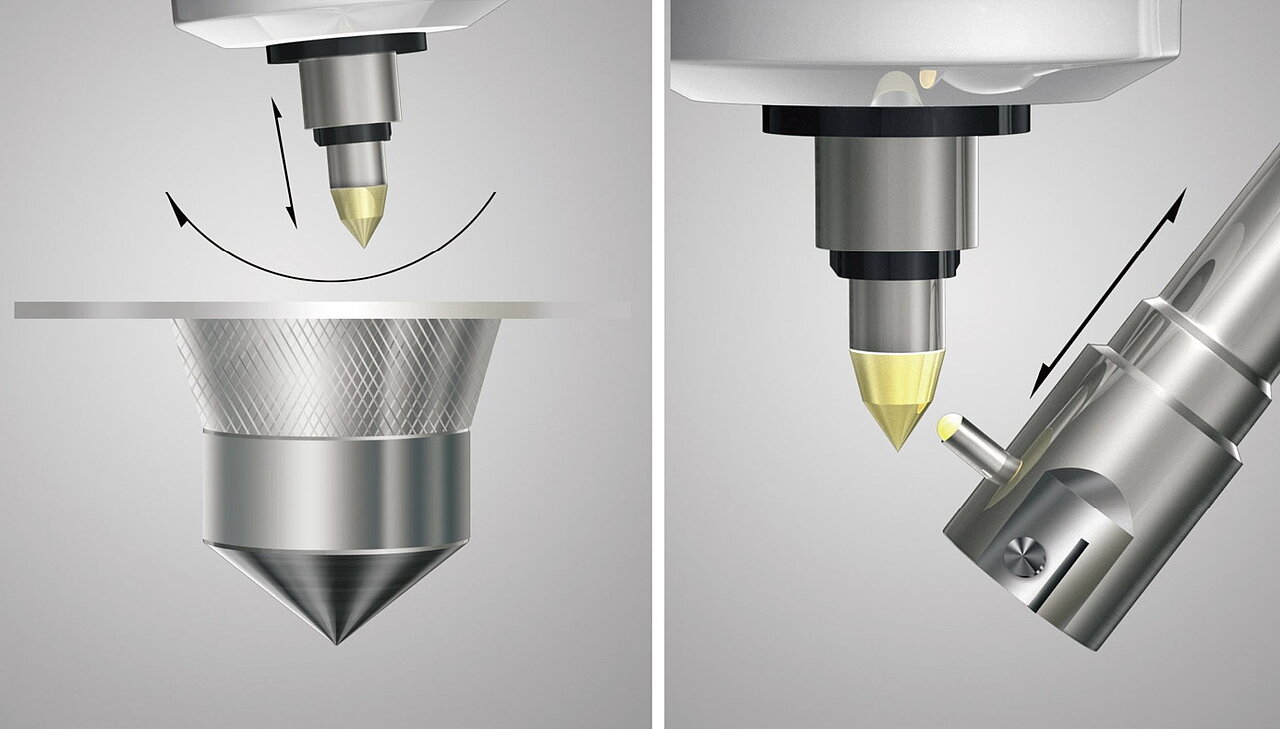
Profimach Centre Hole Grinding Machine - Centre Grinding Machines
In pursuit of Higher Center Accuracy
There is an ever-increasing demand for higher workpiece accuracies.
Running on the dead centre tip of the external grinder the centre bore forms a plain bearing that directly effects the roundness of ground external diamters. For perfect results the taper of the centre bore must be round and co-axial with the centre bore at the other end of the workpiece.
After heat treatment the workpiece centre bores are often out of round or oval, out of alignment, covered with scale and too rough. To obtain good results in cylindrical grinding the centre bores must be ground or lapped by a Centre Grinding Machine before they are presented to the cylindrical grinding machine.
We offer high Quality but Affordable Centre hole Grinding Machines.
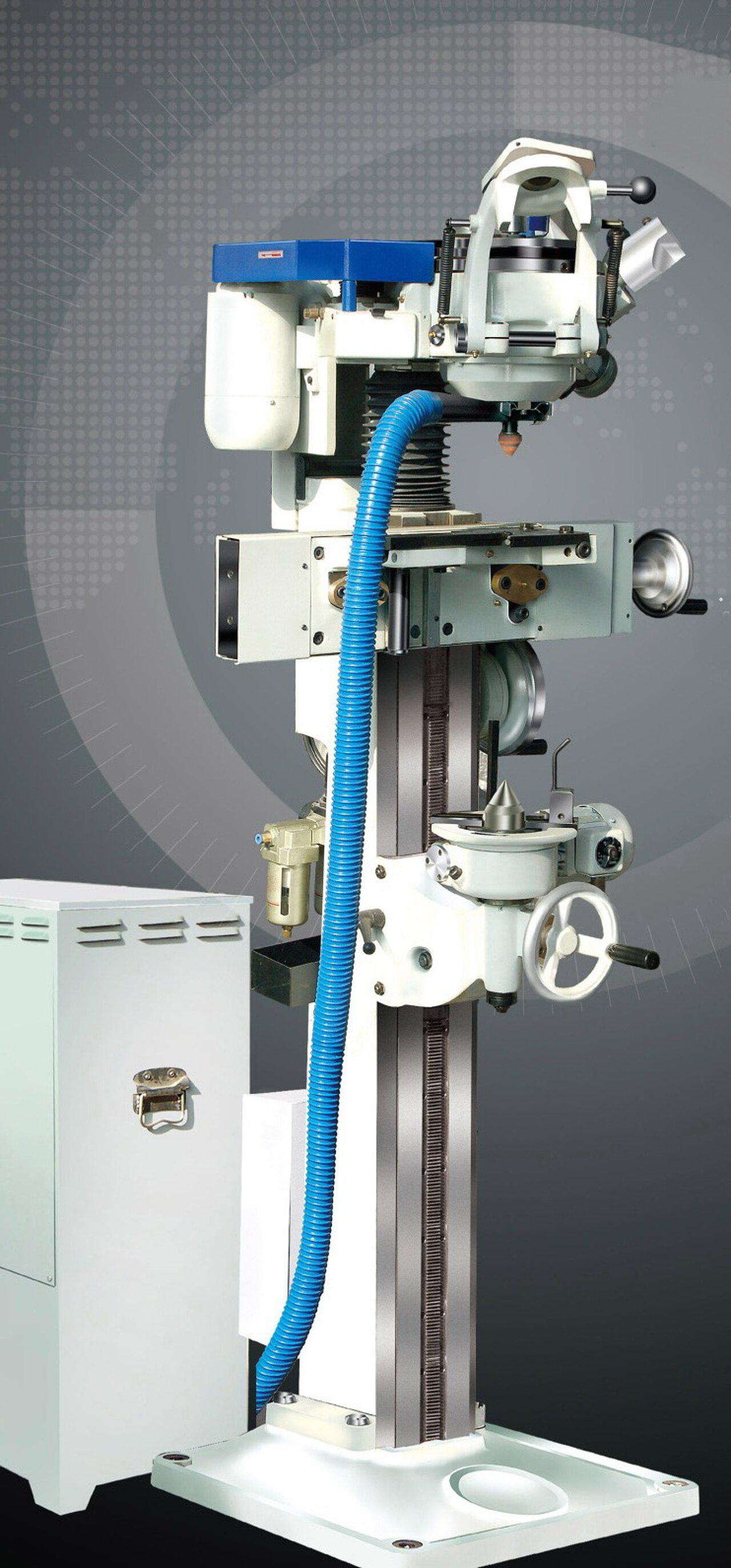
Main machining accuracy:
Center hole cone angle : 60°-4’μm
Surface roughness : ≤Ra0.4
Measure the runout of external circle by locating the center hole : ≤0.002mm
Pursuit of Higher Center Accuracy
Taking advantage of a center hole grinder
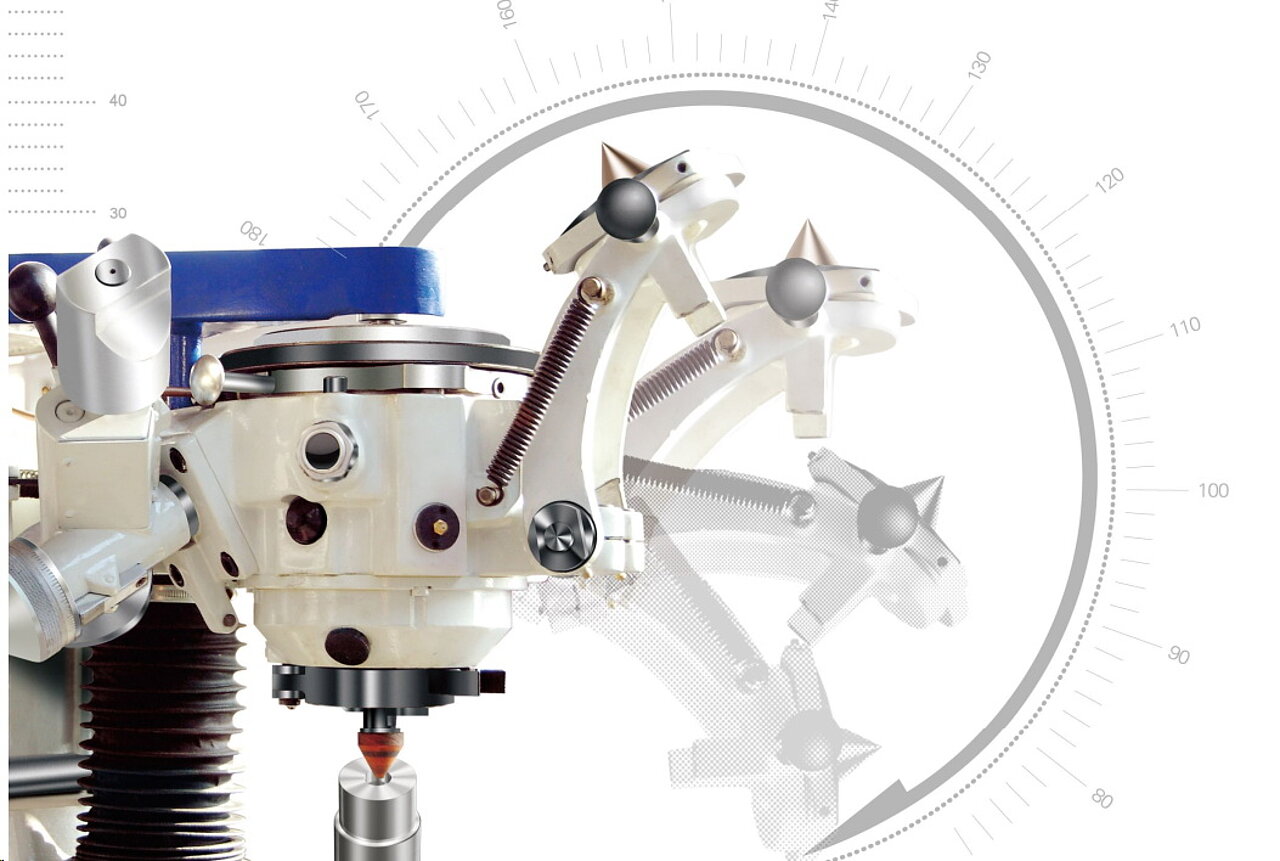
Profigrind | PGCH125M | PGCH180M | |
---|---|---|---|
Main Specifications | |||
Max.Grinding Length | mm | 1000 1500 2000 | 1500 2500 |
Min.Grinding Length | mm | 50 | 100 |
Max.Machining Diameter(normally) | mm | Φ125 | Φ180 |
Max.Machining Diameter(with special equipment) | mm | Φ150 | Φ180 |
Min.Machining Diameter | mm | Φ8 | Φ30 |
Max. Weight of Workpiece | kg | 100 | 250 |
Reciprocating Travel of Wheel Spindel | mm | 0.75~3 | 0.75~3 |
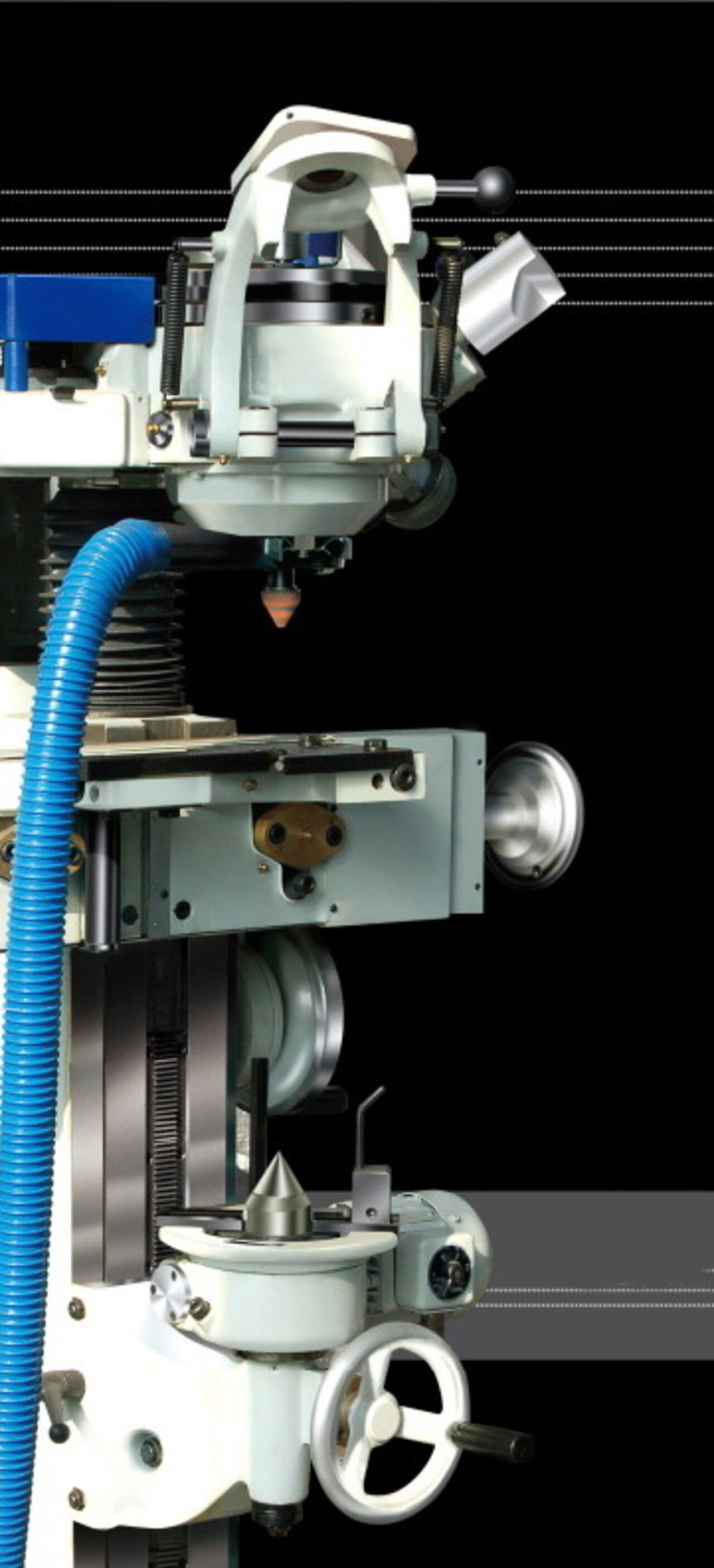
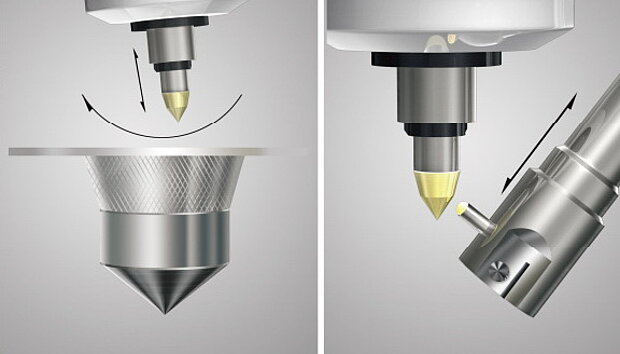
The machine is suitable for cuting tool, spindle, tool holder, gear shafts and tempered transmission shafts and the workpiece requests high accuracy from cylindrical grinding. The quality of cylindrical grinding will depend on the center holes circular geometrical accuracy.
-
Used for workpiece use center holes as positioning for external grinding. The geometric accuracy quality will be increased for cylindrical grinding after center bores grinding.
-
Grinding wheel spindle rotation axis cooperates with planetary axis mechanism. Grinding act could be change against workpiece requirement.
-
Conical swing-down wheel dressing device.
-
Workpiece stationary mode while grinding.
-
Self-centering vice for workpiece holding.
-
Workpiece stationary while grinding, better for its surface.
-
Workpiece drive mode while grinding.
-
3-point steady rest workpiece holder device.
-
Tailstock driving device drive the workpiece while grinding.
-
This type is used with rough surface, high roughness request, bad runout, polygon, hardened or soft workpiece. The center holes do not have to be concentric with the outer diameter.
-
This type is used for workpiece have to run with the external diameter or have to be offset. To ensure concentrically for center bores and external.
- The machine guide way needs many times of aging treatment, good abrasion resistance.
- The grinding shaft components are composed of extremely precise spindle and bearing components. And through a number of aging, flaw detection, processing, assembly and adjustment, and finally in 45000 RPM / sub stable work. Spindle box feed grinding and return.
- The workpiece clamping mechanism has automatic centering function
- Wheel dressing mechanism is moving along grinding wheel semiangle generatrix, accurately dressing the wheel cone.
- The oil mist lubrication is used in the lubrication system, and the oil mist is carry to the workpiece box by the compressed air, to achieve the lubrication of workpiece spindle and bearings.
- The machine is equipped with a vacuum cleaner, which can realize the synchronization of grinding and dust cleaning.
- Electric system
- The wiring is neat, the structure is reasonable, the heat dissipation is strong.
- The electric system is suitable to the working environment.
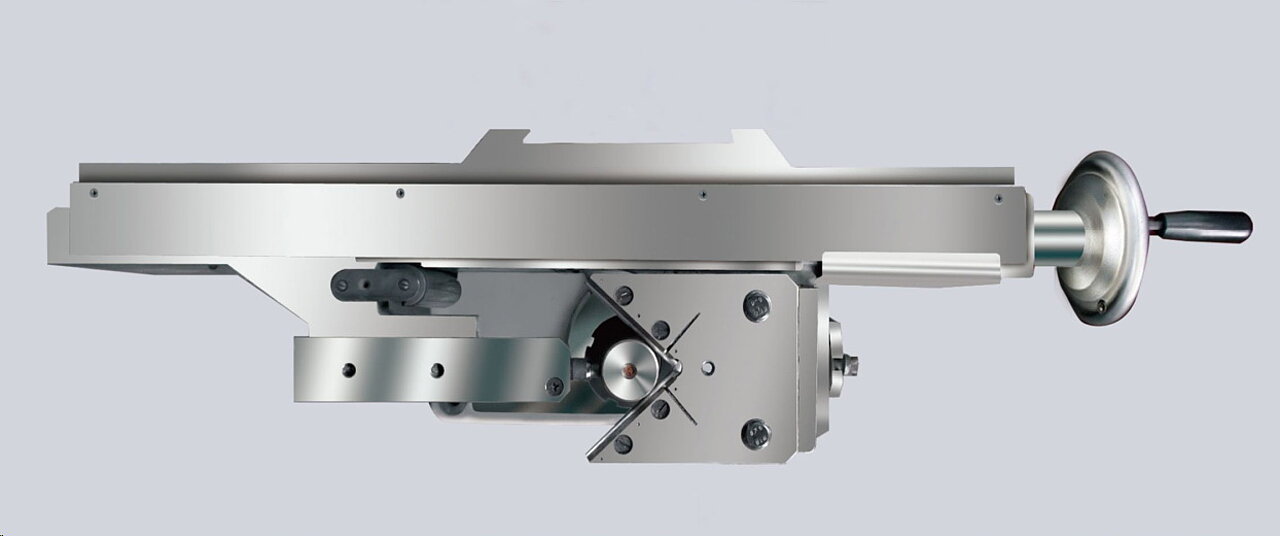